Introduction
The Copper Development Association recommends the copper induction motor over the permanent magnet motor when choosing an electric motor for a Hybrid (HEV) or Plug-in Hybrid (PHEV) electric vehicle. Why?
- High efficiency motors with copper rotors are more economical.
- Copper rotors enable the design of super premium efficiency motors.
- Motors with copper rotors are more compact.
- Copper motor rotors (CMR) offer flexibility to motor manufacturers.
- CMR technology is more established
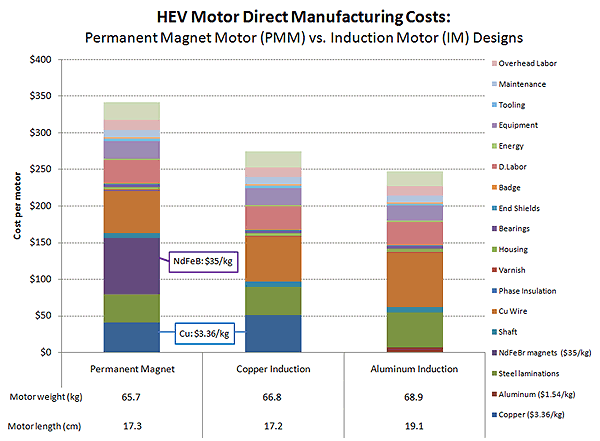
Arguments for Copper Induction Motors
- Copper induction motors offer preferred nominal efficiencies (the value obtained during standardized testing of a number of motors) under normal vehicle operating conditions compared to permanent magnet motors.
- Design and performance simulations conducted by the Department of Electrical Engineering at the Massachusetts Institute of Technology concluded that copper induction motors provide greater efficiency than permanent magnet motors. The operating efficiencies of the cast copper induction motors were 91 percent, compared to 87 percent for permanent magnet motors. (Source: "Improved Hybrid Vehicle Traction Motors Using Cast Copper Rotor Induction Machines," J.L. Kirtley, D.S. Peters, et al, 2008.)
- Permanent magnet motors suffer a drag loss when the motor turns and experience efficiency losses during high speed, low torque operating conditions. Copper induction motors use less energy when not producing torque and are more efficient.
- Induction motors are particularly well suited for hybrid and plug-in hybrid applications because they rely on electric powertrain for low speed, high torque acceleration.
- Copper's superior electrical conductivity makes it ideally suited for the squirrel cage (rotor bars and end rings) in induction rotor motors.
- Permanent magnet motors will not be as cost effective in the future due to concerns over the demand of rare earth oxides outpacing supply. Rare earth oxides are used to make permanent magnet motors. The issue:
- These materials sometimes are referred to as "21st Century gold" for their importance to hybrid car batteries and other high tech applications.
- The future price projections for these materials will depend on current supply constraints and the projected surge in demand for hybrid vehicle motors.
- Copper-based induction motors are 20 percent less costly to manufacture than permanent magnet counterparts with no losses in size, weight or volume.
- The assembly process required for permanent magnet motors requires more steps and is less automation friendly than the high pressure die-casting process used to produce the copper induction motor. For example, the Toyota Prius requires eight permanent magnets to be inserted into the rotor core, followed by compression. The high pressure die-casting process used to produce the copper-based induction motor requires fewer steps (no magnet assembly).
- The demand for greater amounts of permanent magnet motor materials will contribute to further price escalation. Copper induction motors are more cost effective to manufacture.
The manufacturing cost structure of three alternative designs of a 7.5kQ induction motor. Source IBIS
- Permanent magnet motors require a heat exchanger to protect the magnetic materials from demagnetization-adding cost, vehicle weight and reliability concerns.
- Permanent magnet materials may be de-magnetized if motor operating temperatures exceed 200°C (depending on their composition), just 42°C from the estimated maximum operating temperature. For example, the Toyota Prius requires a water-ethylene-glycol heat exchanger, which results in increased cost and vehicle weight while consuming valuable engine compartment volume. (Source: "Comparative Benchmarking Analysis: Hybrid Vehicle Traction Motors" Alan C. Goodrich, IBIS Associates, Inc.) The cast copper induction motor is more reliable, requiring fewer supporting components than the permanent magnet motor. The permanent magnet motor also may experience heat exchanger or boost converter failure.
- Copper induction motors offer improved motor performance during automotive drive cycles.
Conclusion
The copper induction motors are less costly to manufacture than permanent magnet motors, yet provide performance advantages. Permanent magnet motor producers may experience limited global supplies as the demand for materials increases. Copper induction motors offer improved motor performance (efficiency) during automotive drive cycles.