Testing of copper rotors die-cast by the ICA/CDA team during prototyping trials revealed the presence of relatively large amounts of porosity in the end rings of some rotors (see Figure 11.5.1a). Porosity contents as high as 25% were measured, but were more typically in the range of 8-10%. Surprisingly the quality of the conductor bars was generally good ( Figure 11.5.1b). Testing indicated that the electrical performance of these rotors was still good (considerably better than corresponding aluminum rotors), but the presence of such high concentrations of porosity made balancing difficult or impossible.
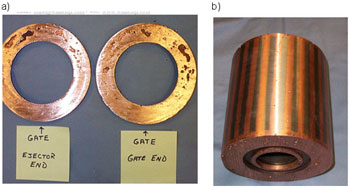
A combination of computer simulations and casting trials revealed that the optimization of two parameters, cavity pre-fill and melt superheat, resulted in a significant reduction in end ring porosity.
11.5.1 Cavity Pre-fill
A computer modeling study was initially performed to evaluate the impact of a number of processing parameters on the level of porosity. The computer package Flow 3-D was used, which uses computational fluid dynamics to simulate the flow of the liquid copper into the die-casting die. Simulation of standard die-casting conditions suggested that large gas bubbles were forming in the gate end ring during the filling of the cavity (see Figure 11.5.1.1). The model was then used to determine which casting parameters had the largest impact on reducing porosity. Parameters examined included injection profile, injection speed, gating type and size, and the amount of cavity pre-fill.
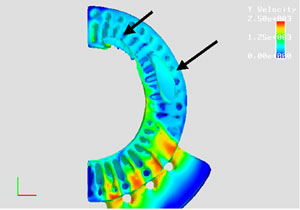
The results from the simulation showed that cavity pre-fill had a large impact on the amount of porosity in the end rings. Cavity pre-fill extends the slow shot so that the liquid copper starts to fill a portion of the die cavity before the fast shot is activated. Figure 11.5.1.2 shows photographs of sectioned end rings taken from rotors cast using different amounts of pre-fill. Clearly the amount of porosity decreases markedly as the pre-fill percentage increases.
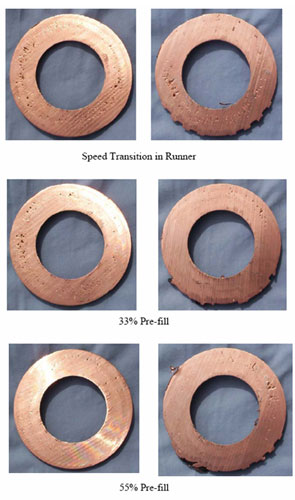
11.5.2 Melt Superheat
The amount of melt superheat was also found to impact the porosity level in the end rings of the rotors. Figure 11.5.2.1 shows photographs of sections of end rings from rotors cast using melt temperatures of 1315, 1365, 1415 and 1465°C (superheats of 232, 282, 332 and 383°C, respectively). Each of the rotors was cast using a cavity pre-fill of 55%. There is clearly a steady reduction in porosity with increasing melt superheat, with no large pores visible on the gate end ring cast at the highest temperature.
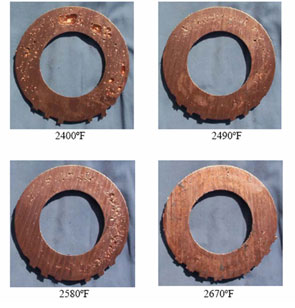
Obviously 2670°C is an extremely high melt temperature and it is not expected that such superheats would be required for commercial production. It should be noted that the dies used to produce these samples were only pre-heated to 120-320°C, while commercial die sets for the casting of copper rotors require that the nickel-based die inserts be pre-heated to about 600°C, and experience with these dies indicate that lower melt superheats are sufficient to obtain adequate part quality. However, the results presented here clearly indicate that heat loss from the liquid copper to the cooler shot sleeve, die inserts and lamination stack must be controlled in order to minimize porosity in the die-cast rotors.
More information on how to reduce porosity in die-cast copper rotors can be found in the Porosity Control in Copper Rotor Die Castings.