Most any die-casting machine can be used for copper rotor casting. However, if a caster is seeking to specify a new die-casting machine for the production of copper rotors, listed below are factors that should be considered. Typically, machines for die-casting copper rotors will have the following requirements:
- Larger-than-normal die height, due to the length of the rotors
- Larger-than-normal ejection stroke, to allow the long rotors to be ejected
- Larger-than-normal opening stroke, to prove space between the die halves for the long rotors to be ejected
- Smaller-than-normal clamping force, due to the limited projected area of the rotor and runner system
- About twice the injection force during die filling as compared to aluminum (due to the high density of the copper)
The companies listed in this section can manufacture machines that meet the special requirements listed above. One die-casting machine manufacturer (THT Presses) has designed their die-casting machines with a vertically upwards injection, especially for the production of rotors. Three other manufacturers (Buhler, BuhlerPrince and Idra Presse) have die-casting machines utilizing horizontal injection, also meeting the specialized requirements of copper rotor die-casting identified above. These four machine designs are described in detail below, and contact information for the three companies is provided here.
11.1.1 Buhler
Buhler is a manufacturer of die-casting machines based in Uzwil, Switzerland. Buhler manufacturers its smaller die-casting machines in Switzerland, while for larger machines the injection systems are build in Switzerland with the clamping systems being built in York, Pennsylvania, USA. Buhler has recently started to build die-casting machines in China, but only for the Chinese market. Buhler serves the worldwide die-casting market with sales and services facilities in about 40 countries on six continents.
Buhler sells die-casting machines ranging in size from 250 tones to 3,500 tones. The Buhler machines incorporate three different shot ends.
- D-machines - the D-machines are designed for conventional aluminum die-castings and have a conventional injection cylinder and intensifier (see Figure 11.1.1.1).
- N-machines - the N-machines have a larger-than-normal injection cylinder together with an intensifier. These machines are designed for semi-solid and squeeze casting applications, where larger injection forces are required. However, the higher injection force provided by the large injection cylinder of the N-machine can provide the large dynamic injection required for copper rotor casting.
- F-machines - Buhler also makes a F-machine, which has the larger injection cylinder, but no intensifier. Under special cases, this could be used to die-cast copper rotors, without the use of an intensifier.

11.1.2 BuhlerPrince
BuhlerPrince is a USA-based manufacturer of die casting machine that is owned by Buhler, but BuhlerPrince makes a separate range of machines (see Figure 11.1.2.1). BuhlerPrince focuses on design flexibility, which allows their machines to be configured to meet the special requirements of copper rotor casting described above. For example, the size of the injection unit fitted to a given machine can be tailored to meet the customer's requirements, providing the higher injection force required when casting copper rotors.
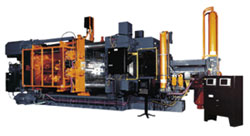
In addition to their normal three-platen style of machine, BuhlerPrince has recently started to manufacture two platen machines that are especially well-suited for the casting of copper rotors. A photograph of the two-platen machine is shown in Figure 11.1.2.2. Rather than using a conventional toggle system for clamping the die, the BuhlerPrince two-platen machines utilize direct hydraulic clamping. Small, low-pressure hydraulic cylinders are used to open and close the die. Once closed, a split-nut is hydraulically closed around groves machined in the tie bars, and high-pressure, large diameter cylinders are activated to clamp the dies shut during metal injection.
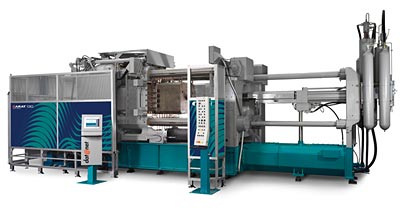
One of the advantages of eliminating the toggle system and the third platen is the greater space now available behind the moving platen for an extra long ejection system. As noted above, large ejection stokes are one special requirement when die-casting copper rotors. The two-platen machines, therefore, can be tailored for the casting of copper rotors.
11.1.3 Idra Presse
Idra Presse is an Italian-based die cast machine manufacturer, with production facilites in Italy and Holland, with about 20 sales reps around the world. Idra also has services centers in Europe (Italy, Germany, UK, Russia) and Asia (China). In addition, Idra has a commercial relationship with Hishinuma, a Japanese manufacturer of small die-casting machines, which provides Idra with an additional sales and service center in Japan.
Idra already has die casting machines producing copper rotors in Europe.
11.1.4 THT Presses
THT Presses is located in Dayton, Ohio, USA and it manufactures die-casting machines used primarily for the production of aluminum rotors. Unlike other die-casting machines, the THT machine has a vertical (upwards) shot and a horizontal die-parting configuration, and it utilizes much larger diameter shot sleeves, plunger tips and shot cylinders than conventional die-casting machines (see Figure 11.1.4.1).
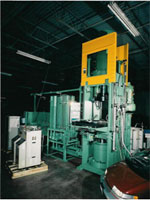
THT Presses is the market leader in North American for the manufacturing of die-casting machines for aluminum rotor casting. In addition, THT now has machines in many countries around the world, in Europe, Asia and South America. THT services these machines through three main service hubs, in South Korea, Brazil and Germany (as well as through their headquarters in the USA).
It should be noted that the high temperature die technology developed by the ICA/CDA to die-cast copper rotors might experience problems when used with the THT machine, as the die design used with this vertical machine utilizes a heavy base plate that is prone to cracking when pre-heated to high temperatures. This issue might be resolvable if a careful pre-heat, design and materials section approach were followed - however this has not been investigated by the ICA/CDA team at this time. THT is reporting, however, that it is currently performing low volume manufacturing of copper rotors at its plant in the USA, although THT plans to move this production to an outside die-caster when volumes become sufficient.
Company Name | Contact Person | Location | Phone Number | E-mail Address | Web Site |
---|---|---|---|---|---|
Buhler | Beni Aschmann | Uzwil, Switzerland | +41-71-955-2734 | Bernard.Aschmann@ buhlergroup.com |
www.buhler group.com |
BuhlerPrince | Mark Los | Holland, Michigan, USA | +1-616-394-8218 | mark.los@ buhlerprince.com |
www.buhler prince.com |
Idra Presse | Roberto Boni | Brescia, Italy | +39 030 20 11 1 | r.boni@ idracasting.com |
www.idra presse.it |
THT Presses | Mike Thieman | Dayton, Ohio, USA | +1-937-898-2012 | mthieman@ thtpresses.com |
www.tht presses.com |