Similar to a die-casting tool for making aluminum rotors, a copper rotor die-casting die consists of a number of cavity inserts assembled into a tool holder. Typical costs for the inserts and tool holder are discussed below.
7.8.1 Cost of the Cavity Inserts
To maximize die life when die-casting copper, it is recommended that the cavity inserts be fabricated from a nickel-based alloy, Haynes Alloy 230. Information about this alloy can be found in Die Materials. These inserts need to be pre-heated and operated at temperatures above 600°C.
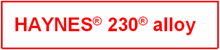
Data generated in the late 1990's showed that the cost of fully machined cavity inserts made from Haynes Alloy 230 were about twice those of similar inserts machined from premium grade H-13 tool steel.
Since that time, however, improvements in die design have significantly reduced the size of the Haynes Alloy 230 cavity inserts required for a copper rotor die. For rotors used in motors up to 30 HP, the cavity inserts used for casting the two end rings now can be extremely small, only 7 to 17 kg in weight. Obviously, this significantly reduces any cost premium associated with using the Haynes Alloy 230.
7.8.2 Cost of the Die Holder
The design of the die holder for copper die-casting should be similar to that used for aluminum rotor casting. Therefore the costs should also be similar.
However, additional costs will be incurred for the extra cartridge heaters (shown below) and insulation required to pre-heat the cavity inserts to 600°C. Information about the cartridge heaters and insulation can be found in Die-Preheating and Control.
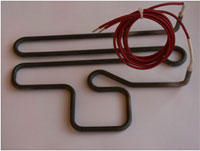