As might be expected, it is not a trivial task to pre-heat and maintain the operating temperature of the cavity inserts at temperatures greater than 600°C. Therefore the design of the casting die is critical. Not only must Haynes alloy 230 inserts be used, but also the positioning of the electrical cartridge heaters and insulation is crucial to obtaining the required temperature in the cavity inserts. Described here are types of cartridge heaters, insulation, and measurement and control systems recommended for use in copper rotor casting dies.
7.4.1 Die Heaters
To maximize the density of heat input to the cavity inserts, the complex-shaped cartridge heaters shown in Figure 7.4.1.1 are recommended. The use of these complex-shaped cartridge heaters allows maximization of heat input to the die inserts, while avoiding die components such as ejector pins and mounting bolts. The cartridge heaters shown in Figure 7.4.1.1 were produced by Hotset in Germany, which has sales offices in 34 countries around the world. Contact information for Hotset is below.

Straight cartridge heaters can also be utilized, and these are also available with their leads attached at 90° (see Figure 7.4.1.2), so the heaters can be embedded deep into the die inserts.
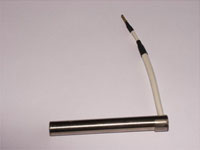
7.4.2 Insulation
To allow the cavity inserts to be pre-heated above 600°C, insulation must be placed between the pre-heated inserts and the die holder, to prevent the larger holder from robbing the heat from the smaller cavity inserts. One type of insulation that is recommended is an insulation board called K-Therm AS 600 M (see Figure 7.4.2.1.), which is produced by AGK Hochleistungswerkstoffe GmbH, located in Dortmund, Germany. Contact information for AGK Hochleistungswerkstoffe GmbH is below.
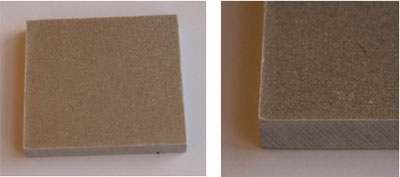
7.4.3 Die Temperature Controllers
Figure 7.4.3.1 shows a photograph of a controller for regulating the pre-heat temperature of the die and die inserts. This eight-channel unit is produced by Xintech, Switzerland.
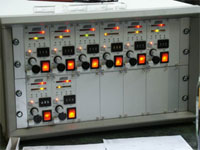
The temperature of the pre-heated dies and die inserts can be monitored by inserting bayonet-style thermocouples into the die. Bayonet-style thermocouples, also manufactured by Xintech in Switzerland, are shown in Figure 7.4.3.2. Similar style thermocouples are available in North America from companies such as Omega.
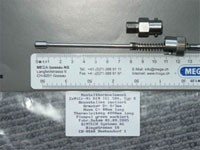
In addition, thermocouples with analog displays can be attached to the surface of the die holder or cavity inserts, to provide a direct reading of die pre-heat temperature (see Figure 7.4.3.3).
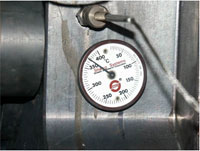
Contact information for Xintech and Omega is below.
7.4.4 Contact Information
Company Name | Location | Phone Number | E-mail Address | Web Site |
---|---|---|---|---|
Hotset | Ludenschied, Germany | +49-2351-4302-0 | [email protected] | www.hotset.de |
AGK Hochleistunge-werkstoffe | Dortmund, Germany | +49-231-936964-0 | -- | www.agk-werkstoffe.de/ index.htm |
Xintech | Dubendorf, Switzerland | +41-1-823-1080 | [email protected] | www.xintech.com |
Omega | USA | +1-203-359-1660 | -- | www.omega.com |