The majority of the die design work during the ICA/CDA copper rotor die-casting project was performed by Ruedi Beck of Dietec AG, a Swiss-based die design company.
Figure 7.3.1 shows a schematic drawing of a rotor die designed by Dietec for use in a horizontal die-casting machine. This design differs from a regular aluminum die-casting die, as the Haynes Alloy 230 cavity inserts are heated to temperatures above 600°C. Various styles of electric cartridge heaters are used to heat the cavities, as described in more detail Die pre-heating & control. In addition, insulation is also utilized in the die design between the cavity inserts and holder die, to prevent heat loss from the pre-heated cavity inserts to the large holder.
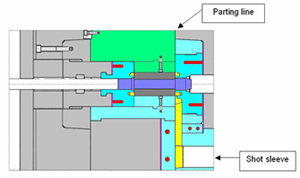
The die components are as follows:
- The rotor steel laminations are shown in dark gray
- The rotor arbor is shown in dark blue
- Copper from the end rings, runner and biscuit are shown in yellow
- The Haynes Alloy 230 die inserts are shown in turquoise (which need to be preheated to >600°C)
- Electrical resistance cartridge heaters are shown in red
- Insulation layers are shown in pink
- The movable slide to allow insertion and removal of the rotor is shown in green
- H-13 or 4140 steel inserts are shown in light gray
During prototyping and production trials performed over the past few years, several advances have been made in the design of the copper rotor dies. These are listed below:
- Instead of bolting the Haynes Alloy 230 inserts to the holder die, the inserts are clamped in place. This simplifies the machining of the Haynes Alloy 230, eliminating the need for threaded holes.
- In addition, the Haynes Alloy 230 inserts are often inserted into the die from the hot face. This allows the inserts to be easily and quickly changed when different sized rotors are to be cast.
- Another recent modification is that the Haynes Alloy 230 inserts themselves are not directly heated, but instead the cartridge heaters are placed into holder blocks, and the heat is transferred to the cavity inserts from these heated holder blocks. Again, this minimizes complex machining of the cavity inserts, and also allows the Haynes Alloy 230 inserts to be kept very small, decreasing the size of the heaters needed for pre-heating, as well as minimizing materials costs.
- Although the die holder is not pre-heated to >600°C (it is generally preheated to about 250°C), a thermal barrier is often required between the die and machine platens, to prevent excessive heat transfer through the platens causing damage to the die-casting machine.
7.3.1 Contact Information
Company Name | Contact Person | Location | Phone Number | E-mail Address |
---|---|---|---|---|
Dietec | Ruedi Beck | Gossau, Switzerland | +41-71-388-2030 | [email protected] |