When die-casting copper rotors using conventional die-casting techniques, the short die life results from the large temperature difference between the pouring temperature of the liquid copper (>1150°C) and the temperature of the die (typically 100-200°C). When the hot copper contacts the die, the resultant thermal expansion of the die surface results in the generation of extremely large plastic strains (1.2% or greater) following each shot. This leads to the rapid onset of heat checking.
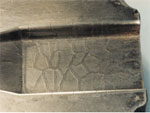
However, if the die pre-heat and operating temperatures are increased to about 600°C, the surface strain can be reduced into the elastic range (less than 0.2%), greatly reducing heat checking and so extending die life. Conventional H-13 die steels will experience problems when heated to such temperatures, due to inadequate high-temperature strength, poor oxidation resistance and the martensite-to-austenite phase transformation that ocurs above 700°C. The most cost effective high temperature die material is a solid solution strengthened, nickel-based superalloy, Haynes Alloy 230.
For those not familiar with the mechanisms causing heat checking, this is summarized below with reference to Figure 7.1.2. When liquid copper is injected into the die ( Figure 7.1.2a), the surface of the die is rapidly heated to a temperature close to that of the liquid copper, resulting in a rapid expansion of its surface layer. However, the interior of the die will initially remain cool, constraining the expansion, and imposing a compressive stress on the surface layer. A short time later, as the copper starts to solidify, heat will start being conducted from the surface to the interior of the die (see Figure 7.1.2b). During the solidification process, the solidified copper rotor will start to pull away from the die surface, limiting heat transfer from the copper ( Figure 7.1.2c), and starting to cool the surface of the die. Once the cast rotor has been ejected from the die, the die surface will cool rapidly, causing contraction ( Figure 7.1.2d). However, as the die interior is now hotter than the surface, the surface contraction is constrained, placing a tensile stress on the die surface.
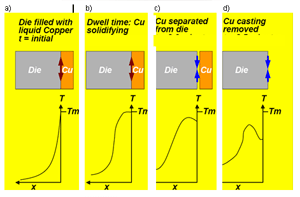
It is this cyclical tensile-compressive stress behavior that causes the heat checking of the die surface. As noted above, computer modeling has demonstrated that harmful plastic strains of 1.2% or greater can be generated at the die surface when liquid copper is injected into a die pre-heated to only 100-200°C. However, when the die is pre-heated to about 600°C, the surface strains are reduced into the elastic range (<0.2%), and heat checking is minimized. Therefore, to achieve extended die life while die-casting copper rotors, it is recommended that the following practices be followed:
- The high melting temperature of copper (1083°C) requires that high temperature, high performance die materials be used. The most suitable die material has been shown to be Haynes Alloy 230.
- To obtain extended die life and avoid premature failure by heat checking, it is absolutely essential to pre-heat and to operate the Haynes Alloy 230 die inserts at elevated temperatures. The optimum temperature range to heat the Haynes 230 dies to is 625 to 650°C. Such high pre-heat temperatures reduce the surface-to-interior temperature differential on each shot, which in turn greatly minimize the expansion and contraction ass°Ciated with each cycle, and thus the thermal fatigue that leads to heat checking.
- It should be noted that pre-heating of die inserts fabricated from conventional H-13 to temperatures around 350-400°C has been shown to provide a modest extension in die life. Empirical data have shown that the die life of the H-13 steel can be extended to over 1,000 shots. Therefore, if only moderate production volume are envisioned, the use of H-13 steel inserts might be economically more attractive.