To optimize the electrical conductivity of copper die-cast rotors, it is necessary to use a copper alloy having very low levels of impurities. As shown in Figure 2.1.1, even low levels of most impurity elements will significantly increase the electrical resistivity of copper.
A range of feed materials can be used with the copper die-casting process, including chopped extruded wire rod, sheared cathode, high quality electrical grade copper scrap or in-house run around scrap (biscuits and runners). Additional details are provided below.
2.2.1 Chopped Wire Rod
Chopped rod made from alloys C10100 and C11000 is available as a commodity in many areas of the world, and typically is only marginally more expensive than sheared cathode. The chopped rod is especially suitable as feed material for single-shot melting. The copper rod shown in Figure 2.2.1 is approximately 12.5 mm (-inch) diameter chopped into lengths of about 19 mm (-inch).
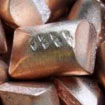
2.2.2 Sheared Cathode
Cathode copper is also available as a commodity around the world, and can be sheared to provide suitable sizes for melt stock.
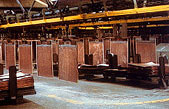
2.2.3 High Quality Electrical Grade Copper Scrap
A third to one-half of all copper around the world is used in electrical engineering or for the supply of domestic electricity. Therefore, scrap electrical grade copper is available in abundant quantities in all developed countries. Oxygen free electronic copper scrap can be obtained from high vacuum electronic applications such as transmitter and waveguide tubes. Suitable electrolytic tough pitch copper scrap includes wire and cable, busbars and electrical windings.

2.2.4 In-House Scrap
Obviously a major source of copper will be from the runners and biscuits used to produced the die-cast copper rotors.
One issue that copper die casters need to be aware of, however, is that the runner and biscuits can become contaminated with metallic trace elements picked up from the die-casting die. Upon subsequent re-melting, these impurities will reduce the electrical conductivity of the copper. Metallurgical testing of die-cast copper rotors has revealed that they can contain small particles of iron or nickel from the die-casting tooling. Such impurities are typically present in the die castings as discrete particles, as they do not have time to fully dissolve during the casting process. However, if these biscuits and runner are subsequently re-melted, the impurity particles will then dissolve in the copper and reduce its electrical conductivity. Therefore, the amount of in-house run around scrap used in each furnace load needs to be controlled, and the composition and electrical conductivity of the melt closely monitored.
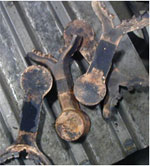