- Introduction
- Heat Exchanger Tubing
- Tubeplates
- Waterboxes
- Evaporator Shells and Flash Chamber Linings
- Piping Systems
- Conclusion
- References
INTRODUCTION
Large scale desalination began with the development of the multi-stage flash (MSF) distillation process in the 1960's. Since then the industry has grown rapidly to become a major user of alloy materials, and in particular Cu-Ni alloys. Installed capacity worldwide by December 31, 1989 was 13,297,000 m3/day.(1) Of this, 62% used the MSF process and although the proportion of MSF plants has declined in favor of other processes such as Reverse Osmosis, it is still favored for large plant capacities such as are required in Middle Eastern countries. The importance of this industry to metal producers can be appreciated from the tonnage of tubing needed to supply the tubing for the installed MSF capacity. This is 210,000 tonnes approximately.
This paper reviews materials requirements for MSF plants and in particular the use of Cu-Ni alloys. Although heat exchanger tubing is the most important individual application, there are other important uses such as tubeplate, water boxes, piping and evaporator shells. The Cu-Nis are used for a wider range of components than any other material in MSF evaporators. The requirements of these components will be considered. Also some of the problems which have occurred in MSF plants will be described. Back to Top
The MSF Process
Figure 1 is a simplified flow diagram of an MSF plant. In this process, evaporation and condensation is split into many stages, thereby increasing efficiency. Incoming seawater is passed through heat exchanger tubing on the exterior of which water vapor, at progressively higher temperatures, is condensing. Finally, it is passed to a heater where steam from an external source supplies the energy for the process and heats the seawater to the maximum process temperature, which depends on the type of anti-scalant used.
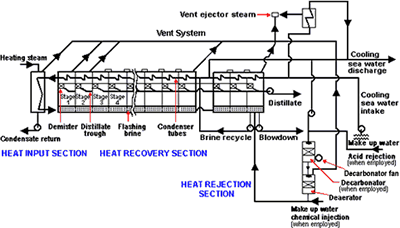
The seawater then passes to the evaporator vessel where pressure is released, causing it to boil or flash. This process is repeated in many stages, the pressure being reduced so that flashing occurs at progressively lower temperatures. The condensed vapor is collected and passed down the plant flashing at each stage and is removed at the lowest temperature and is the product from the plant.
In large plants the major part of the seawater stream is recirculated through the plant. Some is blown down to waste and fresh seawater added to maintain concentration within acceptable limits from scaling considerations. This recirculating brine, because it has been boiled many times, is deaerated and this has a marked effect on its corrosivity. In most modern large plants the feed is deaerated in a separate vessel before adding to the recirculating brine.
The final stages in the plant are known as the heat rejection stages and are the only ones exposed to aerated seawater.
Figure 1 is for a plant where the seawater is acidified to control scaling. It includes a decarbonator to remove the carbon dioxide gas resulting from acidification. When polyphosphates or organic anti-scalants are used, a decarbonator is not required.
MSF is basically a heat exchange process and the tubing should have good thermal conductivity as well as corrosion resistance. Back to Top
HEAT EXCHANGER TUBING
Copper alloys have been traditionally used for handling seawater and this practice was followed when the first large desalination plants were built. The performance of these alloys has, in general, been good and they remain first choice for most plants. Table 1 gives details of the four alloys used.
ALLOY | NOMINAL COMPOSITION 5 | UNS Number | ||||||
---|---|---|---|---|---|---|---|---|
Cu | Zn | Al | Ni | Fe | Mn | As | ||
Aluminium brass | 76 | 22 | 2 | - | - | - | 0.04 | C68700 |
90-10 Cu-Ni | Rem | - | - | 10 | 1.5 | 1.0 | - | C70600 |
70-30 Cu-Ni | Rem | - | - | 30 | 0.6 | 1.0 | - | C71500 |
66-30-2-2 Cu-Ni | Rem | - | - | 30 | 2.0 | 2.0 | - | C71640 |
The choice of alloy depends on the corrosion conditions in the different sections of the plant as well as tube costs. The corrosion conditions can be considered as follows:
1) Natural seawater | - Reject section. |
2) Deaerated seawater and brine | - Brine Heater and Heat Recovery sections. |
3) Incondensable gases and water vapor | - Tube exterior in all sections. |
The behavior of the alloys listed in Table 1 in these environments are described in the following paragraphs.
Back to TopCopper Alloys in Natural Seawater
There is a long and well-documented history of usage of copper base alloys in natural seawater. The most common cause of failure in these alloys is by impingement attack or corrosion-erosion, but many factors such as sulphide pollution, sand in the seawater, chlorination, partial blockage (due to faulty screening or marine growth) etc. can influence this.
A detailed survey of 123 desalination plants was carried out by A.D. Little.(2) The failure rates recorded in this for the reject section were as follows:
Failure Rates* | Tube Costs | |
---|---|---|
Al Brass | 6.8 | Least Expensive |
90-10 Cu-Ni | 2.3 | Least Expensive |
70-30 Cu-Ni | 1.6 | Least Expensive |
66-30-2-2 Cu-NiFeMn | 0.05 | Most Expensive |
* Defined as the percentage of tubes plugged and in retubed bundles |
These data agree with the general experience of these alloys in seawater applications. As the survey covered a large number of plants in many locations it is a reflection of the resistance of the alloys to the many factors given above which influence these alloys in seawater. Sato and Nagata(3) compared aluminium brass and 90-10 Cu-Ni under conditions of partial blockage, chlorination, and sponge ball cleaning. They showed that the 90-10 Cu-Ni was more resistant except with sponge ball cleaning, which should be restricted with that alloy.
In terms of tube costs, the most resistant alloys are the most expensive. For this reason all the alloys listed are used for heat rejection tubing. The 66-30-2-2 Cu-Ni is often used in large plants and is preferred to the 70-30 Cu-Ni which is rarely used in reject sections. For small and medium-sized plants, 90-10 Cu-Ni is normally chosen.
Back to TopCopper Alloys In Deaerated Seawater and Brine
As corrosion of copper alloys in waters of neutral pH requires the presence of oxygen to enable the cathodic reaction to occur, it could be predicted that deaerated seawater and brine would be less corrosive than natural seawater, data from the A.D Little survey support this view. These data are as follows:
Aluminum Brass | 1.07 |
---|---|
90-10 Cu-Ni | 0.38 |
70-30 Cu-Ni | 0 |
66-30-2-2 | 0.02 |
* Defined as the percentage of tubes plugged and in retubed bundles |
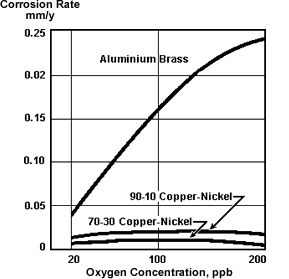
Various studies of corrosion under deaerated conditions have been carried out. Anderson(4) confirmed the beneficial effects of deaeration and found that corrosion-erosion effects could occur at intermediate temperatures even at low (40 ppb) oxygen contents. A study by Dow carried out for the OWRT(5) showed that at low oxygen levels all the alloys tested showed high resistance to corrosion, important differences occurred when the oxygen level increased. Figure 2 illustrates this effect for aluminium brass, 90-10 and 70-30 Cu-Ni. This indicates that aluminium brass is more sensitive to variations in oxygen content which can occur during plant operation.
Effects of oxygen concentration on the corrosion of three copper alloys
in deaerated seawater (90 days at 104C T.D.S. = 35,000 ppm)
Another factor which has to be considered is the effect of pH. Although a low pH will not itself cause corrosion of copper alloys, it can be damaging protective films and allowing the oxygen present to cause corrosion. Evidence for this can again be seen in the data from the A.D. Little Survey, as follows:
ACID | ADDITIVE | |
---|---|---|
Aluminum Brass | 9.0 | 0.02 |
90-10 Cu-Ni | 0.36 | 0.60 |
70-30 Cu-Ni | 0 | 0 |
* Defined as the percentage of tubes plugged and in retubed bundles |
As the normal operating conditions, in terms of pH, for acid and additive dosed plants is very similar, the differences in failure rate can only be due to operating outside the design values which is possible with acid dosing. Again, the Cu-Nis are more consistent in performance under fluctuating plant conditions.
Another section of the plant which is exposed to deaerated conditions is the brine heater. This section is exposed to the highest plant temperature – up to 120°C. Experience has shown that the tubing in this section has the highest failure rates but when the tubes are examined they are seen to have failed by scaling or due to damage during mechanical descaling, corrosion failures are rare. For this reason it is usual to fit 70-30 Cu-Ni tubing in this section because of its higher strength and ability to withstand mechanical descaling. In some cases the reason for failures has been misinterpreted and thin-wall titanium was fitted which resulted in a shorter life than the original copper alloy.
Back to TopCopper Alloys in Incondensable Gases
The gases evolved from flashing brine pass into the vapor space, are guided to the gas extraction zone by baffle plates, and the concentrated gases are then removed by steam ejectors. These gases are mainly carbon dioxide and air (oxygen and nitrogen). In acid-dosed plants most of the carbon dioxide is removed before the seawater is fed to the plant, but in additive-dosed plants, the heat of the process decomposes bicarbonates and much greater amounts of carbon dioxide are evolved.
Seawater normally contains a small amount of ammonia, and this also passes to the vapor space increasing the corrosivity of the gases. Some designers vent the Brine Heater into Stage 1, and if ammonia-forming compounds, such as hydrazine, are used for boiler water treatment, this markedly increases the ammonia content of the bases in the vapor space. Although this ammonia is not a problem in the Brine Heater, as oxygen is absent, it can cause serious corrosion on the copper tubing in the high temperature stages where some oxygen is normally present.
Although there have been some reports of corrosion on tube exteriors in gas extraction zones (Sato and Nagata(6)), the main problem encountered is an increase in copper content in the product water. In one case known to the author this increased to 2.5 ppm, whereas in most plants, it is less than 0.02 ppm.
There is little information on gas concentrations in vapor spaces. Conventional thinking is that most gas is removed in the first few high temperature stages. However recent(7) work on corrosion of carbon steel in MSF plants shows that air inleakage, together with gases cascading down the plant and from flashing distillate, can cause severe corrosion.
Experience from power plant condensers is that 70-30 Cu-Ni is the best copper base alloy for resisting corrosion in the gas extraction zone. This alloy is often used for his section even when the unit is tubed with another alloy.(8) Tests in ammonia/carbonate mixtures(9) demonstrated the superiority of 70-30 Cu-Ni in these environments. Data from these tests are as follows:
Alloy | Corrosion Rate (mm/year) |
---|---|
Aluminum Brass | 0.13 |
90-10 Cu-Ni | 0.10 |
70-30 Cu-Ni | 0.08 |
In MSF plants 70-30 Cu-Ni is often selected for the top temperature recovery stages, especially when additive anti-scalants are used, in order to resist the high concentrations of carbon dioxide and other gases in these stages. As aluminium brass can suffer stress corrosion cracking(2) due to ammonia in incondensable gases, this alloy is not normally used in the high temperature stages although sometimes used in the low temperature recovery stages.
Where vapor side corrosion occurs, it causes uniform thinning of the tube wall, eventually resulting in perforation. There may be some pitting associated with the thinning but this is normally very shallow and does not cause penetration. Vapor-side corrosion is most frequently experienced in vent condensers where incondensable gases removed from the plant are cooled before exhausting to atmosphere. In these units the life of copper alloy tubing is short - a few years - and titanium or high alloy stainless steel is used.
Back to TopHeat Exchanger Tubing - Trends in Materials Selection
Based on the considerations reviewed above the optimum materials selection for copper base alloys would be:
Preferred Alloy | Alternatives | |
---|---|---|
Heat Reject | 66-30-2-2 Cu-NiFeMn | 70-30 Cu-Ni |
90-10 Cu-Ni | ||
Aluminum Brass | ||
Heat Recovery | 70-30 Cu-Ni (Top stages) | 90-10 Cu-Ni |
90-10 Cu-Ni | Aluminum Brass | |
Brine Heater | 70-30 Cu-Ni | 90-10 Cu-Ni |
Some plants using 66-30-2-2 Cu-NiFeMn in the reject sections also use this alloy in the Brine Heater and the high temperature recovery stages. Although this is technically satisfactory, this alloy is a little more expensive than the 70-30 Cu-Ni, which is preferred.
Back to TopTUBEPLATES
The normal method of fitting tubes into MSF plant is by roller expanding into tube plates. These plates are subjected to corrosion conditions similar to the tubing and are made from similar copper-based alloys. However, as these plates are relatively thick, as compared to the tubing, sometimes other less expensive alloys are used. Table 2 gives details of some tubeplate materials often used in desalination plants.
Alloy (UNS Number) | Tubeplate Materials - Nominal Composition % | |||||
---|---|---|---|---|---|---|
Cu | Ni | Al | Fe | Zn | Sn | |
90-10 Cu-Ni (C 70600) |
REM. | 10 | - | 1.5 | - | - |
Aluminum Bronze (C 61400) |
REM. | - | 7 | 3 | - | - |
Naval Brass (C 46400) |
REM. | - | - | - | 39 | 1 |
When Cu-Ni tubing is used, 90-10 Cu-Ni is the preferred tubeplate material. Aluminium bronze is less expensive than 90-10 Cu-Ni and has higher mechanical properties (which can be advantageous by allowing a reduction in plate thickness); hence, its use in this application.
Naval brass is the least expensive of the alloys listed but is less corrosion resistant than the others. In natural seawater it can suffer dezincification, despite its tin content to limit this; but, this can be controlled by fitting iron anodes in the water boxes.
90-10 Cu-Ni and aluminium bronze have good weldability and can be welded directly to the steel shell which simplifies construction. Naval brass can be welded only with great difficulty and is usually bolted to the shell.
90-10 Cu-Ni is available as clad plate i.e., a steel plate with an integrally bonded layer of Cu-Ni. Where this is used with roller expanded tubing, an adequate layer of alloy must be provided in order to achieve a tight connection. This layer should be 8-10 mm thick, which means that this type of tubeplate is economical only for thick constructions. A thinner layer is possible if the tubes are welded into the tubeplate, but this is not normally used for MSF plants.
If an inadequate alloy layer is used and a leaking tube to tubeplate joint results, corrosion can occur on the carbon steel behind the alloy layer. This results in the development of a large pit or hole in the steel, and the corrosion product diffuses to the tubeplate surface along the leaking joint. On this surface, a large tubercule of rust forms. In aerated seawater this is mainly ferric oxide, but in deaearated conditions it is usually black magnetic iron oxide. The early stages of this type of corrosion show themselves by evidence of red or black iron oxides "bleeding" from the expanded joint. Cleaning off and re-expanding can sometimes prevent further corrosion.
Back to TopWATERBOXES
MSF plants require water boxes and, in cross-tube plants, the number required can be large. Because of the large area of copper base alloy provided by the tubes and tubeplates, galvanic corrosion can occur if carbon steel is used for the water boxes. Coatings have proven unreliable, with the exception of thick (3-5 mm) rubber linings which are sometimes used in the reject section. Damage to coatings can result in concentration of attack at the damaged area resulting in rapid penetration. Also coating breakdown has resulted in partial blockage of the tubes giving local turbulence and tube failure.
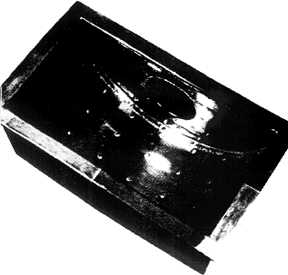
Most large modern plants use water boxes made from 90-10 Cu-Ni clad steel plate. The alloy layer is usually 2.5-3 mm thick. This thickness is set by fabrication considerations – the ability to work with tolerances within the thickness of the alloy layer. Corrosion considerations would allow a thickness of about 1 mm which is adequate for the tubing.
90-10 Cu-Ni has good weldability. Inert gas welding is preferred, although coated manual electrodes are available. In both cases, the filler material is usually 70-30 Cu-Ni to ensure that the less homogeneous cast structure of the weld matches the corrosion resistance of the wrought base material. The filler metals and electrode coatings must contain small amounts of elements with a high affinity for oxygen and nitrogen. These are usually manganese and titanium. Full details of welding these alloys, including clad products, are given in (10).
Figure 3 illustrates a technique which has been used to line components with 90-10 Cu-Ni. This involves the use of metal inert gas welding to provide a spot weld to fasten the lining to the steel component (11) gives details of this technique which has been used for lining water boxes and other MSF plant components. Thin sheet (1.2 mm) is used for water boxes.
Back to TopEVAPORATOR SHELLS AND FLASH CHAMBER LININGS
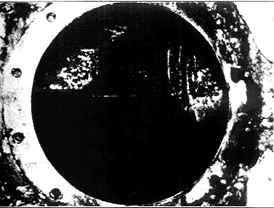
90-10 Cu-Ni has been used for construction of evaporator shells – usually in small plants up to 1,000 tonnes/day. It has also been used for lining large plants, notably the 50 mgd Al Khobar plant in Saudi Arabia where all stages are lined with alloy. In this case, 90-10 Cu-Ni clad plate was used for the shell with solid alloy for internal components.
In small plants advantage is taken of the ability to weld Cu-Ni direct to carbon steel by using relatively thin Cu-Ni for the parts exposed to corrosion and providing strength with external steel sections. This gives an economically attractive, high quality construction which has been proven over many years of service life. Figure 4(12) shows a plant which operated in Ascension Island for over 20 years. The 90-10 Cu-Ni evaporator body, water boxes, etc., were in excellent condition with no evidence of corrosion damage.
In large plants, corrosion of steel in flash chambers has been a serious problem,(13) and most plants are now partially - sometimes completely - lined with alloy material. Although it is accepted that plants with alloy linings are more reliable and require less maintenance, the economic aspects are often questioned. A study(14) on this aspect concluded that a plant completely lined with 90-10 Cu-Ni would cost only 5% more than an unlined one. If this is true for all plants, then the use of linings must be economic.
The choice of lining materials is between stainless steel and 90-10 Cu-Ni. Although both are technically satisfactory, the stainless steel is slightly less expensive. However, this saving is offset by the extra care needed to avoid pitting during shutdowns when oxygen has access to the plant. Both materials, therefore, can be accepted for large plants, and both are specified.
Paint coatings have been tried in an attempt to provide a less expensive lining. These have not been satisfactory as the paint film is damaged by the equipment which has to be used inside these plants for routine maintenance. Repair to the coatings is often difficult to fit into the shutdown schedule, and pitting at damaged areas usually results. In some cases breakdown of paint coatings has resulted in blockage of pump filters, necessitating unscheduled plant shutdown for cleaning.
Back to TopPIPING SYSTEMS
Large amounts of piping are required in MSF plants to carry seawater, brine, etc. Various materials, including steel, coated steel, 316L stainless steel, FRP and 90-10 Cu-Ni are used for these pipes. While steel is cheap in first cost, it suffers from corrosion and requires maintenance and replacement. In seawater, 316L stainless steel suffers pitting and, although it can be used in deaerated seawater and brine, care is needed during shutdowns to avoid leaving chloride-containing water with access to oxygen. Coated steel is unreliable and FRP has given problems.(15)
90-10 Cu-Ni has been used for piping systems for many years. It is technically suitable for use in both aerated and deaerated seawater and brine, but its economic suitability is sometimes questioned. In this connection, a UK study(16) which carefully examined all factors influencing pipe costs, (design, fabrication, installation etc.), is of value. This showed that the installed cost of a ship's seawater system in 90-10 Cu-Ni was only 30% more expensive than a system in cast iron and steel, even though the material costs for the alloy system was 3 times that of the steel system. As the steel system would require renewal at least once in the life of the ship, then the alloy system was clearly more economic.
Considerations similar to those used in the above study(16) apply to MSF piping and to 90-10 Cu-Ni piping systems which are widely used in these plants and have performed well. These considerations include good weldability, ability to use high flow velocities (minimizing pipe size and cost), and ready availability of standard pipe fittings.
Back to TopCONCLUSION
The Cu-Ni alloys have a combination of properties, such as corrosion resistance, fabricability and mechanical properties which meet the needs of MSF plants. These alloys, particularly 90-10 Cu-Ni, have been used for a wider range of applications than any other material. Also, their performance in these applications has generally been good. Further development of this industry is likely to involve more use of these alloys even when new processes are used. This is because seawater is likely to be the main feedstock for desalination and the Cu-Nis have a proven record for handling seawater. Back to Top
REFERENCES
- K. Wangnick. 1990 Worldwide Desalting Plant Inventory. "The Development of the Desalination Market." 12th International Symposium on Desalination and Water Re-use. Malta Apl. 1991. Vol 1.
- "Survey of Materials in Large Desalting Plants Around the World." March 1972 - E. H. Newton, J. D. Birkett and J. M. Ketteringham. A. D. Little Report to the US Office of Saline Water.
- S. Sato and K. Nagata. "Evaluation of Various Heat Exchanger Tubes for MSF Plants." Sumitomo Light Metal Tech. Rep. 1977, Vol 18, Nos. 1/2, pp. 11-20.
- D. B. Anderson. INCO Publication No. 4319. "Cu-Ni and Other Alloys for Desalination Plants."
- "Desalination Materials Manual." Dow Chemical Company for The Office of Water Research and Technology, USA.
- S. Sato, K. Nagata, T. Kanamori, Y. Shiota, N. Hirashi and C. Y. Kwong. "Corrosion Survey of Aluminium Brass Heat Exchanger Tubes in Acid Dosed Desalination Plant." Sumitomo Light Metal Tech. Rep. 1981, Vol. 22. Parts 3/4, pp. 1 - 12.
- J. W. Oldfield and B. Todd. "Vapour Side Corrosion in MSF Plants." Desalination, 66 (1987) pp. 171-184.
- S. Sato, K. Nagata and S. Yamuchi. "Evaluation for Various Preventive Measures Against Corrosion of Copper Alloy Condenser Tubes by Seawater." Paper No. 195. Corrosion 81. Toronto Apl 1981.
- E. A. Tice and C. P. Venizelos. "Corrosion Behavior of Condenser-tube Alloy Materials." Power Nov. 1963.
- NiDl Publication 1280. "Guide to the Welding of Cu-Ni Alloys."
- W. F. Ridgway and D. J. Heath. "Lining Mild Steel Components with 90-10 Copper-alloy Sheet." Welding and Metal Fabrication. Oct 1969.
- D. A. Rayney."NICKEL." Vol. 6, No. 3, p. 11. March 1991.
- J. W. Oldfield and B. Todd. "Corrosion Considerations in Selecting Materials for Flash Chambers." Desalination, 31 (1979).
- H. E. Hoemig and B. R. Soeltner. "Reliability in Estimating Costs for Large MSF Plants." Proc. IDEA Congress Oct. 1979.
- F. B. Seraphim. "Operation of Three Seawater Desalination Plants." BSE/NACE Corrosion Conference Bahrain, Jan 1981.
- D. Bailey. "The Economics of Materials Usage in Seawater Systems." Project No. G30, May 1982.