Copper Contributes to Big Engines that Can
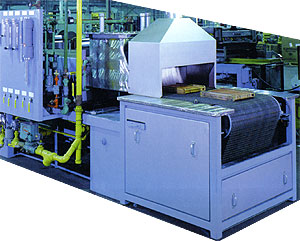
Copper-brass radiator cores can be brazed nearly twice as fast as aluminum cores thanks to the new CuproBraze™ process shown here. Installed at Universal Auto Radiator Manufacturing Company, Pittsburgh, the process is expected to create cores that "... will cost at least 10% less than comparable aluminum cores," says Johan Scheel, vice president of the International Copper Association, New York. ICA sponsored development of the new process. In addition to lower cost, the Cuprobraze differential between the brazing and melting points of brass is 300° C. In contrast, when aluminum is brazed, the differential between the brazing and melting temperatures of the metal is only 40° C. Because of Cuprobraze's much greater temperature tolerance, there's very little chance of damaging the output, and the processing equipment can operate faster, another big advantage. The CuproBraze™ process not only takes up one-third less floor space than aluminum brazing but does not require the fluxing and washing operations of the latter, freeing additional useful work space. Dozens of international radiator manufacturers have already inspected the process, which is expected to begin commercial production in a few months. Brazed copper cores are both lighter and stronger than comparable copper cores assembled by soldering.
Also in this Issue:
- Versatile Prepatinated Copper
- Copper Scales New Heights
- Copper Is Cooler for Cars
- Copper Contributes to Big Engines that Can
- Wiring for Today’s High-Tech Homes
- Undersea Oil Platforms Rigged with Copper