High-Efficiency Motors Pay Off
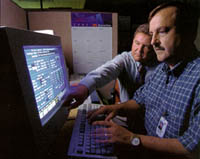
After cutting annual energy costs by $823,000 at its headquarters complex in St. Paul, it's no wonder the 3M Company is extending optimizing of electric motor systems to its other facilities. A good fraction of the savings can be ascribed to replacement of old, lower efficiency motors with the latest 1-dgh-efficiency premium motors.
Nationwide, replacement of old, lower-efficiency motors with the latest, high-efficiency premium motors makes great sense, because half of all the electricity generated in the U.S. is consumed by motors. In addition, premium motors are not only more efficient (mostly because they are made with more copper), they also last much longer and generate less heat.
An important stimulus to motor replacement efforts is the U.S. Department of Energy's "Motor Challenge Program" (see sidebar). The program was fostered by the Energy Policy Act of 1992, which calls for new standards for efficiency, testing and labeling for power-consuming products, including integral horsepower motors.
Many companies are already enjoying the benefits of motor replacement including fast payback. For instance, at 3M Company's headquarters, payback on the motor-optimizing program took a bit less than two years. According to Steve Schultz, a senior project leader in 3M's Facilities Engineering and Real Estate Department over the past two years 280 motors were replaced.
Most of the replaced motors, which ranged in size from 3 up to 100 hp, were powering the heating, ventilating, air conditioning (1-fVAC) systems in the 25-building complex. However, a few were also in processing plants.
Adjustable-speed Drives
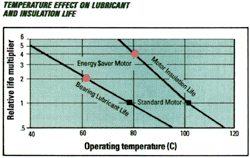
All of the premium motors installed for 3M are from General Electric. Inn many instances in HVAC systems, adjustable-speed drive replaced constant-speed drives whose output was controlled by dampers or valves. By eliminating dampers and valves and relying only on changes in speed to control ventilation, less energy is expended on heating or cooling. This resulted in additional savings comparable to the reduction in costs derived from the motors themselves.
"In some instances, we replaced existing motors with high-efficiency inverter duty motors to obtain a high degree of reliability for certain motors being operated from adjustable-speed drives," says Schultz.
The 3M Motor Challenge Team in charge of replacement was pleasantly surprised in several instances when the new motors drew even less power than calculated. However, in one instance, Schultz discovered that the premium-efficiency replacement drew more power than the old motor. The problem was in the sheaves attached to the fan: once they were resized to compensate for the lesser slip of the new motor, it proved even more efficient than anticipated.
Dismounting old motors considered candidates for replacement to bench check their efficiency is a costly and time-consuming procedure. That's why the 3M team relied on a method of calculating efficiencies in place developed at Stanford University, Palo Alto, California. Calculating efficiencies has now been made much easier, because it's available on PC software from the Motor Challenge Program, Olympia, Washington (see sidebar). The manufacturers of motors, including GE, also provide software to help in specifying motors.
Motor Challenge Program: 800/862-2086
Free Guidance in Saving Energy
Want to cut company power charges big time? Then concentrate on integral horsepower motors by contacting the Motor Challenge Information Clearinghouse in Olympia, Washington. This office, sponsored by the U.S. Department of Energy, does much more than provide free software to determine the efficiency of motors, essential in deciding whether or not to replace. Its ten technicians are also available at 800/862-2086 with advice at no charge on getting the most out of motors, according to Robert Penney, Clearinghouse lead engineer. The office is open weekdays from 6 a.m. to 5 p.m. Pacific Standard Time.
"MotorMaster" software lists the name-plate efficiency of some 12,000 motors ranging from 1 to 600 hp manufactured according to the standards of the National Electrical Manufacturers Association, including some made outside the U.S. For unlisted motors-or unlisted motors whose hp rating may fall below that given on its nameplate-the software helps calculate their efficiency based on voltage, amperage, power factor, load and rotational speed under load.
To use the three-disk software requires a PC with Windows 3.1 or 95 and at least 8 MB of RAM, but 16 is recommended. It occupies 16 MB of hard drive. A 98-page user manual is provided with the software. However, those who need help in mastering it can call the office. Classes in using the software are also available. Since the Motor Challenge Program was launched in 1994, over 1,600 organizations have signed on.
Care Needed in "Rewinding
Instead of replacing old, lower-efficiency motors (and any premium motors) that burn out, many owners save money by replacing the copper coils in-their big motors. According to Wallace P. Brithinee, head of Brithinee Electrical, a motor-repair shop in Colton, California, the common break-even point in deciding whether to rewind or replace is 60-65% of the cost of replacement. Above that, replacement is the rule.
However, rewinding must be done carefully by qualified shops that adhere to standards, or there's a possible loss in efficiency. To remove old windings and insulation from the stator laminations, they haveto be heated. One of the risks in removal is that excessive heat is employed in the burnout oven. Overheating the laminations degrades their electrical properties, thus 11 decreasing efficiency.
In one example, the efficiency of a conventional 75 hp motor driving a conveyor belt originally rated a- t 90.8% dropped to an unacceptable 67% after improper rewinding, according to experts from General Electric's Motor Division. To avoid such waste, the experts urge companies to contract for rewinding only with member firms of an organization dedicated to quality electrical repair, the Electrical Apparatus Service Association. It has 2,500 members, including 225 in Canada.
Brithinee, whose shop rewinds about a thousand motors, a year, claims that careful rewinding should result in very little loss of efficiency. His shop is able to rewind premium motors rated up to 100h hp to within 0.5% of their original efficiency; on the largest motors, those rated in the hundreds of hp, motors are rewound to within 0.25% of original efficiency.
Electrical Apparatus Service Association: 314/993-2220
Brithinee Electrical: 909/825-7971
Also in this Issue:
- Copper Helps Attract High-Tech Tenants to Wall Street
- High-Efficiency Motors Pay Off
- Tough, Bright, Beautiful Finishes
- UL's Highest Winds Can't Topple Copper Roofing