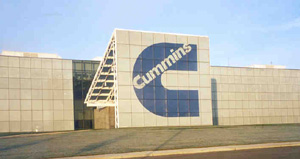
Mention Cummins engines to anyone who's ever put the pedal to the metal in an 18-wheeler and you'll probably hear words like value and efficiency. Cummins engines typically run for a million and a half miles between overhauls, and four to five million total isn't unusual. As for efficiency, the company can rightfully claim industry-leading fuel economy and power-to-weight performance, especially in new models like its ISM engine, introduced in 1998.
It shouldn't come as a surprise, then, that Cummins also practices energy efficiency in its plants. It does so very aggressively; in fact, energy efficiency is part of the company's corporate philosophy. Cummins management believes a proactive energy efficiency policy helps the company stay competitive.
And they're right. Cummins' energy savings have been so remarkable that the U.S. Department of Energy's (DOE) Office of Industrial Technologies (OIT) granted the company its Industry Captains Command Award in 1999. DOE/OIT bestows the award on forward-thinking companies like Cummins who reduce energy consumption while at the same time creating real benefits to the environment.
This article describes how Cummins did just that while saving more than $200,000 per year in energy costs. And yes, those savings wouldn't have been possible without copper.
It Began with an Energy Survey
Good ideas sometimes come at you from where you least expect them. In Cummins' case, their award-winning energy program began in their Midrange Engine Plant, located in Walesboro, Indiana. The plant had been shut down in the 1980s but was brought back to life in 1987 when the company began producing 100,000 engines annually for Daimler Chrysler's popular Dodge Ram pickup trucks.
Public Service of Indiana (PSI), the local utility, surveyed the plant to determine where Cummins could reduce its energy consumption things like better lighting and more efficient air handling. Many utilities offered this service-known as demand-side management or DSM-in an effort to forestall the need for new power plants.1
A number of beneficial changes came out of PSI's survey, but most important, it introduced Cummins to the DOE's Motor Challenge program. Motor Challenge is a highly successful government effort to help American industry optimize its energy-efficiency, maintain competitiveness and reduce greenhouse gas emissions. Since electric-motor-driven equipment consumes about 70% of all electricity produced in the country, increasing motor efficiency by even a few percent quickly adds up to big savings nationwide.
How big? Consider this: While conferring an Industry Captains Command Award to Cummins, OIT program manager Paul Scheihing noted that "If every plant in the United States integrated motor system upgrades to the extent that Cummins did, American industry would save $1 billion annually in energy costs. This would be the equivalent of the amount of electricity supplied to the State of New York for three months."
Energy efficient motors produce big paybacks... fast!
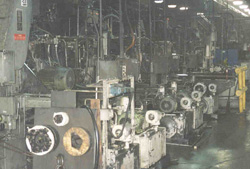
Cummins began its active involvement with Motor Challenge in 1995, focusing on its 1.4-million-square-foot main plant in Columbus, Indiana and the 296 motors that drive the plant's engine block machining and transfer lines. The plant's production lines are veterans, having turned out hundreds of thousands of Cummins' industry-standard 365- to 525-hp N14 (and other) engines over the years. While the lines' electric motors were reliable enough, their efficiency ratings were typical of those available 30 years ago.
"What do you do with 296 old motors, especially when they're still running well?" recalls Tim Burke, director of administration/finance for Cummins' MidRange Central Purchasing office. "We studied the information provided by the Motor Challenge program thoroughly. In the end, we got to the point where we realized we'd be better off throwing these things out."
That meant getting rid of more than 1,000 motors, including those that were in service as well as all spares.
Cummins brought in the McBroom Electric Company of Indianapolis to take a close look at every motor on the production lines. McBroom is a large motor distributor, a long-time supplier/contractor to Cummins and an active allied partner in the DOE's Motor Challenge program.
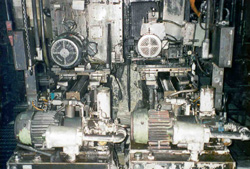
McBroom's audit projected that Cummins would save $80,000 per year in power costs by replacing all of the lines' 1- to 125-hp standard efficiency motors with premium-efficiency motors.2
Faced with that amount of savings, Cummins decided to upgrade the line. At the time, however, both Cummins' agreement with PSI's Synergy program and the company's own internal capital allocation obligations required that an investment of the size envisioned must realize a payback of two years or less. Therefore, when Cummins' plant engineers specified the upgraded motors, they were very interested in verifying the projected results.
Cummins replaced 296 motors ranging from 1 to 125 hp with premium-efficiency U-frame motors manufactured by U.S. Electrical Motors, a division of Emerson Electric Co., The premium motors' windings contain more copper than standard motors, making them a few percent more efficient than the standard motors they replaced. The improved efficiency was sufficient to reduce Cummins's power costs for the machining and transfer line by $80,000 per year.
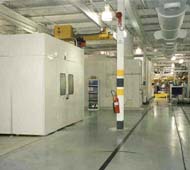
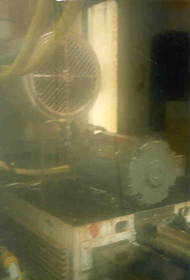
Figure 3. Cummins Engine constructed a 230,000-sq ft state-of-the-art machining and assembly line at its Columbus, Indiana plant in 1995-1996. The new line produces up to 280 heavy-duty Signature 600 truck engines per day. Machine tools are mounted in mist-collection enclosures such as those shown at left. The detail shows two of the line's 500 premium-efficiency motors.
Maintenance manager Howard Stogdill recalls: "We made a great effort to keep the same motor sizes and types for the motors we replaced. We also wanted to maintain uniformity in our new equipment, so we specified that all replacement motors must be of the U-frame types manufactured by U.S. Electrical Motors, Inc." (U.S. Electrical Motors is a division of Emerson Electric Co., Inc.)
Table 1 shows the results of Cummins' motor-upgrade program. They provide dramatic proof that improved efficiency yields big savings.
Motor Size (hp) | Motor Quantity | Total Horse Power | Total kW | Savings |
---|---|---|---|---|
1-25 | 245 | 2,385 | 1,779 | - |
30-100 | 49 | 2,420 | 1,805 | - |
125 | 2 | 250 | 187 | - |
Total | 296 | 5,055 | 3,771 | $79,869 |
McBroom's forecasts were right on target. According to Tim Burke, "Our experience since the upgrade showed that the premium-efficiency motors reduced our annual energy costs by the amounts expected, and the savings we realized paid back our investment in less than two years."
Rob Boteler, director of marketing for U.S. Electrical Motors, agrees. "Cummins Engine's engineers took steps that demonstrate their understanding of motor driven systems. They analyzed costs over the motor's life cycles and implemented one of the most aggressive programs in America to optimize energy efficiency. By taking advantage of the latest developments in efficient-motor technology, they enabled their machines to use the least amount of energy to do the work required and, at the same time, returned the highest level of value to their shareholders."
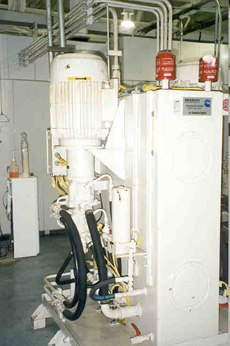
In 1995, Cummins began expanding their Columbus plant, adding 230,000 square feet of manufacturing space for new machining and assembly lines. Because of the spectacular savings gained by upgrading motors on their existing machining and transfer lines, Cummins engineers insisted that the new lines be equipped with premium-efficiency motors as well.
Angela Ferguson, the plant's controls engineer, led the effort, again calling for premium-efficiency U-frame motors from U.S. Electrical Motors. Ferguson specified motors for all equipment serving the new lines, including 24 machine tools, lubricant and coolant pumps, as well as ventilating and de-misting equipment. The work entailed 500 motors ranging in size from ½ hp to 200 hp.
"We used MotorMaster+ to spec the motors. McBroom Electric, our motor vendor, supplied the motors directly to the equipment OEMs," recalls Ferguson. "Ordinarily, the OEMs would have installed standard-efficiency motors to lower their costs, but we wouldn't let them do that. At the time (1996-1998), there weren't even good definitions of what we call premium-efficiency motors available, but we went by criteria set in EPAct, or higher. We knew we'd have to give up certain technical features in order to get energy-efficient motors, but all in all the motors have performed more reliably than the standard-efficiency motors we were using before. Of course, the energy-efficient motors cost more initially, but they paid for themselves with lower operating costs in less than two years.
"As for specifying the same types of motors we'd installed in the earlier upgrade, it just made sense to standardize on one motor type and one supplier. Continuity and predictable reliability are important in a production situation like ours. We prefer U-frame motors because we've found they give longer life than T-frame types."
It is important to note that EPAct does not apply to U-frame motors of the type specified by Cummins' Ferguson. By insisting that the new U-frame motors nevertheless meet or exceed EPAct efficiency requirements, Ferguson was going beyond the letter of the law to ensure that her company took advantage of the best current technology to realize the maximum energy savings possible.
Did the new energy efficiency motors save money? You bet they did! The 500 new motors Ferguson specified in place of standard OEM motors paid for themselves in less than two years. Table 2 (below) shows the breakdown of the $128,000 in annual energy savings Cummins realized when it installed the motors in its new machining and assembly lines.
Motor Size (hp) | Motor Quantity | Total Horse Power | Total kW | Savings |
---|---|---|---|---|
1/2-25 | 372 | 1,354 | 1,010 | - |
30-100 | 119 | 5,450 | 4,066 | - |
125-200 | 9 | 1,300 | 970 | - |
Total | 500 | 8,104 | 6,046 | $128,042 |
What Do Those Savings Mean Overall?
Cummins' Tim Burke knows. "After retrofitting energy-efficient motors on our existing machining and transfer lines and installing the most efficient motors available on our new lines, we've seen a 2.75 percent reduction in total energy costs for the Columbus plant. We think that's very significant because those lines constitute only a portion of our energy usage for the entire plant."
Cummins believes in copper... and not just in it's energy efficient motors. Its new assembly line is powered using all-copper bus bar. In addition, the company plans to network its major machine tools with their production control and inspection departments. So when the new line was built, all equipment and electrical and data/communications systems were properly grounded using copper grounding conductors. Proper grounding is extremely important to ensure error-free data communications.
Cummins Looks at Environmental and Other Benefits
Burke is convinced the energy-efficient motors were a smart choice. "We actually have an in-house-developed corporate standard for life-cycle costing of equipment. We call it USIRR. The IRR stands for internal rate of return. We've put USIRR in use throughout the corporation. We use standard interest and tax rates in our calculations, which we carry out over a 10-year analysis base.
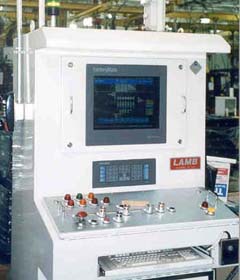
"In the case of the energy-efficient motors, energy savings provided the major incentive, of course, but since installing the motors, we've discovered other benefits. For one thing, we now have all new motors in our upgraded transfer lines, so maintenance costs have been reduced. We also like to think of Cummins as an environmentally friendly company - it's one example of what we call our Customer-Led Quality Initiatives. We can now point to the reduction in fossil fuel use and lower greenhouse gas emissions brought about by our energy-efficient motors as evidence of our corporate environmental awareness."
That sounds like a win-win-win-win situation for Cummins and the environment.
- Lower life-cycle costs, even in a low energy cost region
- Fewer breakdowns, lower maintenance costs
- Lower fossil fuel consumption and reduced green-house gas emissions
- A proactive, positive corporate energy strategy that supports a good corporate image.
Defining " Efficiency " of Electric Motors
Motors with improved electrical efficiency are still relatively new products, and terminology regarding "energy-efficient" and "premium-efficiency" motors remains somewhat unclear. A brief explanation of this terminology may therefore be helpful.
Recognizing that electric motors on average use about 60% of the electicity used in industry in the U.S.A. and that improving motor efficiencies would therefore have a significant effect on over-all energy consumption, Congress enacted the Energy Policy Act of 1992 (EPAct). The Act was signed into law by President Bush on October 24, 1992 and became effective for motors Oct. 24, 1997. Among its many other stipulations, EPAct mandates that certain motors sold in the U.S.A. after the effective date of the Act must be of "Energy Efficient Design."
Specifically, according to Department of Energy publication DOE/GO-10096-312, EPAct applies to "General purpose, T-Frame, single-speed, foot-mounted, continuous-rated, polyphase, squirrel-cage, induction motors of National Electrical Manufacturers' Association (NEMA) designs A and B. The subject motors are designed to operate on 230/460 V and 60 Hz and have open and closed enclosures. EPAct applies to 6-pole (1200 rpm), 4-pole (1800 rpm), and 2-pole (3600-rpm) open and enclosed motors rated 1 through 200 hp."
"EPAct does not apply to definite-purpose motors (i.e., those designed for use under unusual conditions or for use on a particular type of application which cannot be used in most general applications) or special-purpose motors (i.e., those designed for a particular applications with special operating characteristics or mechanical construction)."
The Act mandates that motors meet the minimum efficiency ratings listed in NEMA Standard MG 1-1993, Table 12.10. EPAct recognizes NEMA Standards and IEEE/ANSI 112-1991 Test Procedures. 3
Energy-efficient motors take advantage of a number of improvements to reduce operating losses, but their most important physical difference is that they incorporate a larger cross-section of copper in their windings than is found in old standard-efficiency motors.
Resistive losses in a motor (which show up as wasted heat) are governed by the formula:
P = I² R
where P is the power consumed, I is the current drawn and R is the resistance of the windings. A decrease in resistance results in a reduction in losses. Increasing the cross-sectional area of the copper windings reduces losses and makes the motor more efficient.
The actual ROI realized by upgrading to an energy-efficient motor depends on a number of factors, including the prevailing cost of electric power. Plants that operate in high -power -cost locations will naturally realize higher savings and better ROIs. In Cummins' case, however, their plants are situated in one of the lowest energy cost areas in the nation. Despite enjoying rates as low as $0.04/kWh (the nationwide average is more than 50% higher), the amount of money the company saved by replacing old standard-efficiency motors convinced Cummins they were on to a good thing.
Better Yet...
While the minimum efficiency ratings defined under EPAct and NEMA MG 1-1993 represent a significant improvement over older motors, it should be noted that motor technology continues to progress. In recent years, the term "premium efficiency" has come to denote motors whose efficiencies exceed the EPAct standards, generally by between one and four percent. One organization that has defined the term "premium-efficiency" for use of its members is the Consortium for Energy Efficiency (CEE). A copy of the CEE guidelines is available from Copper Development Association Inc.
Like Cummins Engine, your company can benefit from the greater energy savings provided by energy-efficient electric motors. A good place to start is to request more information about the Motor Challenge Program. Contact:
Office of Industrial Technologies
Energy Efficiency and Renewable Energy
U.S. Department of Energy
Washington, DC 20585
The Principals
Timothy J. Burke is Director - Admin/Finance of Midrange Central Purchasing, Cummins Engine Company, Columbus, Indiana. In addition to providing financial support to engine business purchasing operations, he is responsible for material cost improvement, budgeting and capital tracking/analysis. His financial analysis supported the purchase of premium-efficiency electric motors. Mr. Burke holds a BA in Economics from the Indiana University College of Arts and Sciences.
Angela G. Ferguson is a Controls Technical Specialist with the Cummins Engine Company, Columbus, Indiana, where, among other responsibilities, she has been a key player in the design, procurement, installation and start-up of a cylinder block and head machining line. Selection of premium-efficiency motors was an integral part of that responsibility. Ms. Ferguson holds a BSEE from Purdue University and is currently pursuing a Masters Degree in Manufacturing Management.
Howard Stogdill is Maintenance Manager at the Cummins Industrial Center, Seymour, Indiana. A journeyman electrician, Mr. Stogdill supervised the replacement/installation of premium-efficiency electric motors at Cummins' Columbus Engine Plant.
Cummins Engine Company, Inc., is the world's leading manufacturer of diesel engines rated at more than 200 hp and the second largest supplier of diesels larger than 50 hp, making the $6.3 billion Columbus, Indiana, company the world leader in medium and large diesel power plants. While it is best known for its widely used truck and off-road-vehicle engines, Cummins is also a leading manufacturer of diesel engines for emergency and standby power plants, as well as marine and industrial engines rated up to 3,200 hp. Further information is available by writing to: Corporate Headquarters, Cummins Engine Company, Inc., Columbus, IN 47202-3005.
Footnotes
1. A number of electric utilities currently offer DSM programs. For Further information, contact CDA.
2. The term, "standard efficiency motors," as used here, refers to motors sold before full implementation of the Energy Policy Act of 1992 (EPAct).
3. It is important to note that the NEMA efficiency ratings for motors sold in the USA are based on actual operating data under dynamometer-controlled test conditions. Efficiency ratings for motors sold outside the USA may be based on less stringent test standards than those used by NEMA, and non-U.S. efficiency ratings therefore tend to be overstated.