Download PDF Version [885 Kb]
- Experimental Plan
- Gains… and Some Losses
- Influence of Centrifugal Loads
- Payback and Long-term Savings
- Lower Operating Temperatures
- Conclusions
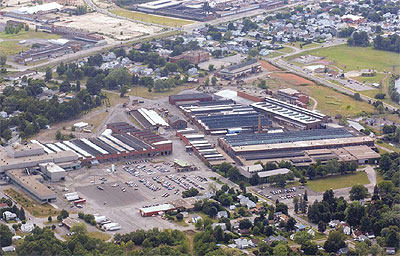
Photo courtesy of Revere Copper Products
This summary describes the results of a copper-rotor motor evaluation program undertaken by the New York State Energy Research and Development Authority (NYSERDA) at the Rome, New York, brass mill of Revere Copper Products, Inc. A companion summary report describes another portion of that program conducted at the Menands, New York, water treatment plant of the Albany County Sewage District.
NYSERDA initiated the program in 2006 to quantify the economics of replacing old but fully serviceable motors with ultra-high efficiency copper-rotor motors (CRMs). The authority utilizes data of this sort for a program that provides incentives to motor users. In addition, the evaluation program measured operating temperatures of several motors under known loading conditions.
The Copper Development Association (CDA) administered the contract and hired Advanced Energy Corporation, a Raleigh, North Carolina-based certified laboratory, to conduct the analyses at both sites. The full reports are available from NYSERDA or CDA.1
Experimental Plan
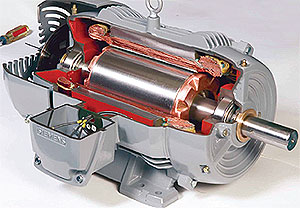
Photo courtesy of Siemens AG
Measurements were taken on the old motors’ kW consumption, current, voltage, power factor, time-load profiles and operating temperatures, along with flow rate or pressure (in hydraulic applications). The same data were taken on new motors. Measurements were taken at one-minute intervals over a 2½-hour period. Ambient and motor operating temperatures were measured by Mohawk Valley Predictive Technologies using an infrared technique.
Following reference data collection, old motors were sent to Advanced Energy’s laboratory for physical characterization, including efficiency testing to IEEE Standard 112, Method B, and determination of energy-load profiles. This action was taken because the old motors had been rewound one or more times, and nameplate data were unreliable. Energy-load profiles for the copper-rotor motors were provided by the manufacturer (Siemens).
Back to TopGains … and Some Losses
Average nameplate efficiency of six of the ten existing motors for which numbers were available was 86.63%. Advanced Energy found the average measured full-load efficiency to be 86.24% and that the operational efficiency was 86.69%.2 The extensive data analyzed by Advance Energy are omitted here to save space, but are in the report to NYSERDA. The full-load efficiency data are consistent with the small decrease one would expect for rewound motors of this age. Operating efficiencies are slightly higher than full-load nameplate expectations since operation occurred nearer the peak in the power curve.
Dataplate efficiencies of replacement copper-rotor motors ranged from 91.7% at 7.5 hp to 93.6% at 20 hp, averaging 92.42%. The average measured full-load efficiency of the new motors was a nearly identical 92.45%. (CDA has previously reported3 that Siemens rates its copper-rotor motors conservatively.) However, the average calculated operational efficiency of the CRMs was only 89.08%, because four of the motors were being operated at or less than 12% of full rated load, which is far from the optimum utilization.
Despite those clearly oversized motors, the average operational efficiency of the new CRMs was almost 2.4 percentage points higher than that of the motors they replaced. Nevertheless, of the 10 motors installed at Revere, one-half yielded negative savings (losses) compared with the old motors when calculated for a utility rate of $0.14/kWh.
Influence of Centrifugal Loads
All motors selected for evaluation drove centrifugal loads, generally pumps or blowers. In such cases, shaft power is proportional to the cube of rotational speed — the so-called cube rule. CRMs operate with lower slip and, therefore, higher speed than conventional motors. That caused them to draw more power, which offset the gains made by the CRMs’ higher efficiencies. In extreme cases, the results were energy losses.
Centrifugal loads, such as fans, can be slowed with inexpensive pulleys; whereas, pumps are more effectively controlled by slowing the CRMs with variable frequency drives (VFDs). The drives negate the slip/speed penalty and the resultant losses in economic benefits. The NYSERDA program took this effect into account and included in its evaluation additional measurements on motors equipped with a VFD.
Projected savings using VFDs with CRMs were calculated for four motor-pump combinations in which loading conditions between old and new motors were similar. Calculations showed that these four CRMs would generate positive annual cost savings. It was realized after the fact that six of the applications in the motor replacement program had large load variations over time, making comparison of power consumption between old and new motors meaningless.
Payback and Long-term Savings
A two-year payback is generally acceptable. In addition, in view of the longer service lives expected for CRMs, the projected 10-year savings derived from an investment in high-efficiency CRMs (with VFDs) can be significant. The project examined these savings, including replacing an old motor with other improved types, including NEMA Premium® and EPAct motors.4 The results listed below assume $0.14/kWh, the peak rate paid by Albany County in 2008, and $0.09242/kWh, the average rate paid when the study began in 2006. The rate paid at Revere was not known.
The first three examples in the Revere plant yield payback times between 30 and 37 months at $0.14 per kWh, but the 10-year cost savings amount to several thousand dollars in each case. The cost of the VFD doubles payback times over those for the cost of the new motor alone. CRMs Nos. 2 and 3 (see table below) drive water pumps and No. 6 is a filter media vacuum pump, all directly coupled. For pumps, there is no simpler and cheaper way to reduce the speed by a few percent than a VFD.
Motor No. 9 drives a blower. Here, an inexpensive modification to the pulley and belt drive system may well suffice. Assuming the cost of this modification is negligible, pay-back periods are still rather long, and the 10-year cost saving is slightly negative for the lower of the two electricity rates used here.
Energy savings and payback periods were calculated using MotorMaster+, versions 3.0 and 4.00.06 for EPAct and NEMA Premium motors, respectively.
Centrifugal loads must be examined carefully. Correcting for the higher speed of the CRM with a VFD significantly increases energy savings but requires a larger up-front capital expenditure. For large motors with high duty cycles, the CRM leads to larger 10-year energy savings than replacement with either an EPAct or NEMA Premium motor. For motors with low duty cycles driving centrifugal loads, the CRM + VFD combination does not appear to be cost effective at the utility rates considered here.
Motor | Replacement Cost Motor + VFD ($) | Ann. Energy Savings (kWh) | Ann. Energy Cost Savings ($) | Electricity Rate ($/kWh) | Payback Period (Yrs / Mos) | 10 year Cost Saving ($) |
---|---|---|---|---|---|---|
No. 2 15 hp, 1800 rpm |
936.00 + 953.35 | 5,339 | 747.46 | 0.14 | 2.5 / 30.3 | 5,585 |
493.43 | 0.09242 | 3.8 / 45.9 | 3,055 | |||
No. 3 15 hp, 1800 rpm |
936.00 + 953.35 | 4,305 | 602.60 | 0.14 | 3.1 / 37.6 | 4,137 |
397.87 | 0.09242 | 4.7 / 57 | 2,089 | |||
No. 6 15 hp, 3600 rpm |
952.25 + 953.35 | 5,345 | 748.30 | 0.14 | 2.54 / 30.5 | 5,577 |
493.98 | 0.09242 | 3.86 / 46.3 | 3,034 | |||
No. 9 10 hp, 3600 rpm |
693 + 0 | 702 | 98.28 | 0.14 | 7.06 | 289 |
64.88 | 0.09242 | 10.7 | - 45 | |||
Source: Advanced Energy Corporation and Copper Development Association. |
Lower Operating Temperatures
The new CRMs operate significantly cooler than the old motors, which is important because heat degrades winding insulation and thereby shortens motor life. An accepted rule of thumb states that a 10°C increase in operating temperature reduces a motor’s life by half. Bearing life is also adversely effected.
Temperature measurements were taken in both plants, while the new CRMs and old motors were operating at what, at the time, were thought to be identical loads. Identical temperature guns were used for the measurements. Revere, in addition, employed infrared imaging through a third party vendor, results of which are shown below.
Conclusion
The NYSERDA evaluation program clearly demonstrates the value of replacing old, less-efficient motors with higher-than-NEMA Premium copper-rotor motors, and that replacing EPAct–era or even NEMA Premium motors can also be recommended under certain circumstances. Replacements should be considered in terms of both payback periods as well as long-term savings, since individual situations may influence the results differently. The program also underscores the need to consider concurrent installation of a VFD when centrifugal loads are anticipated. These devices add to initial cost but can provide substantial savings over time. Finally, the NYSERDA program confirms the cooler operating temperatures expected in the more efficient copper-rotor motors, which suggests that they should enjoy longer service lives.
Ambient | Max Temp. (AR01) | Max Temp. (AR02) | Rises (Above Ambient) |
---|---|---|---|
22.1°C | 71.5°C | 66.7°C | 49.4°C/44.6°C |
Infared Image: I1117-01 | Digital Image: 5820 | ||
![]() |
![]() |
||
Ambient | Max Temp. (AR01) | Max Temp. (AR02) | Rises (Above Ambient) |
22.1°C | 71.5°C | 66.7°C | 49.4°C/44.6°C |
Infared Image: I1117-01 | Digital Image: 5820 | ||
![]() |
![]() |
||
Source: Mohawk Valley Predictive Technologies |
Footnotes
The New York State Energy Research and Development Authority, In-Plant Demonstration of Electrical Energy Savings Realizable with the Copper-Rotor Motor, Contract No. 10241, Joseph, C. Borowiec, NYSERDA Project Manager, Prepared by Dale T. Peters, Copper Development Association Inc., August 2009.
For calculation methods, see Reference 1 and Agamloh, Emmanuel B., The Partial-Load Efficiency of Induction Motors, IEEE Trans. on Industrial Applications, Vol. 45, No. 1, January/February 2009.
Copper Motor Rotor Update, Copper Development Association, November 2006.
The Energy Independence and Security Act of 2007 raises mandated motor efficiency standards from those of EPAct 2002 to NEMA Premium levels effective in December 2010. Data for EPAct motors in the table assume such motors are available from inventory.