Somersault Letterpress: Continuing the Legacy of Handcrafted Copper Letterpressing
The love story that is Somersault Letterpress is told in metal and grease, at a pace that resists the industry’s push for speed and embraces a process that elevates the craft of printing. And more often than not these days, proprietors Amy Pienta and Mitch Hansen, turn to copper dies whenever they foil or emboss with their 1963 Heidelberg Windmill platen press.
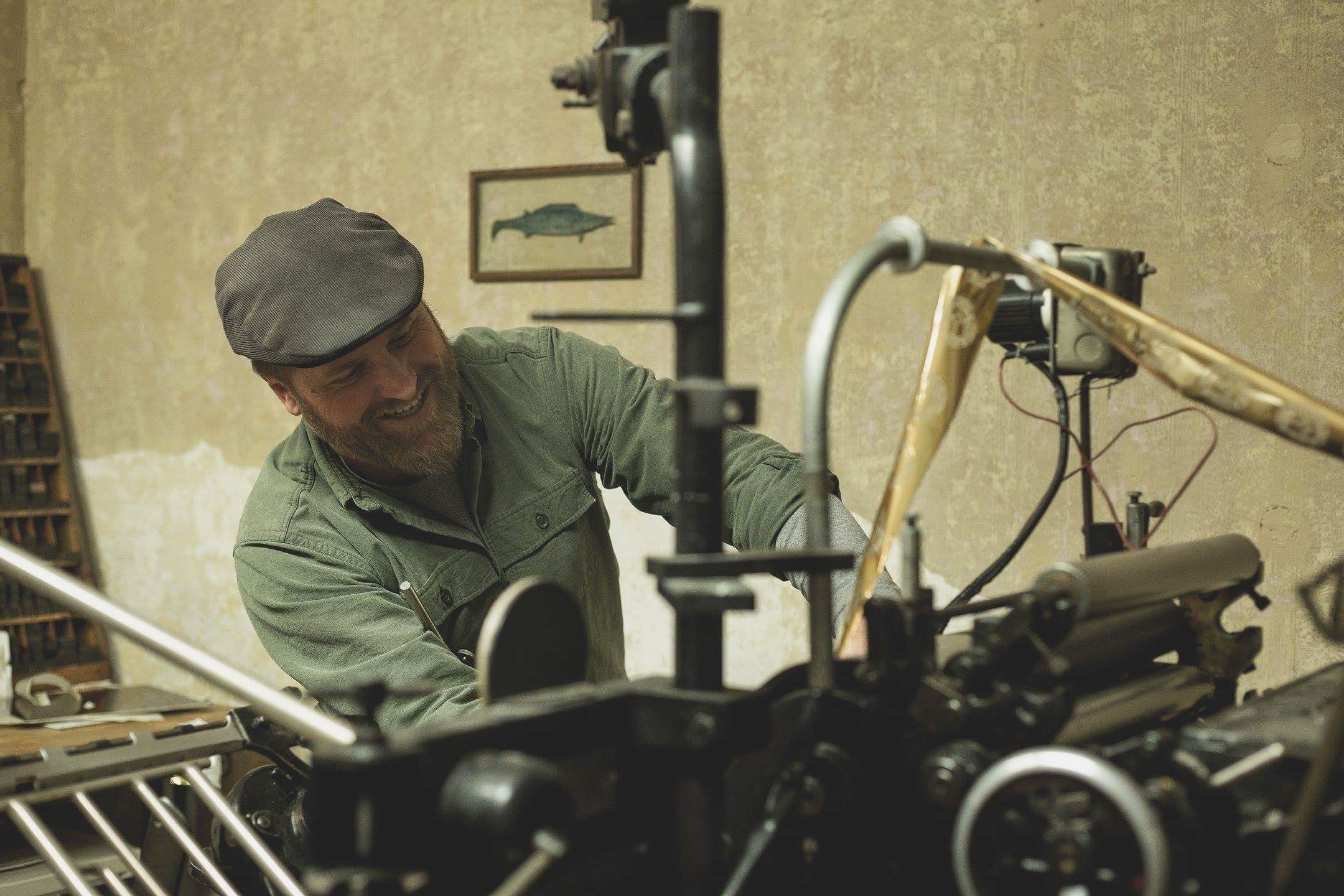
Windmill platen press.
Photograph courtesy of Somersault Letterpress.
Somersault Letterpress is an award-winning letterpress serving luxury and business marketing clients across the country from Jim Thorpe, PA where the couple are testing the edges of their craft.
“We tend to use many different, colored paper stocks and because our inks for letterpress printing are translucent,” says Pienta. “Hot foil is a great way to bring a lighter color in to darker paper or just the right amount of shine when using metallic foils.”
Hansen’s expert execution of Pienta's designs is found in the precision afforded by the dies.
“When we foil on press, we are using heat and pressure,” Pienta says. “Copper dies are a great choice because of their strength. The hardness of the metal allows us to use the right amount of pressure to flatten out the paper in order to achieve smooth foil lay-down and crisp detail.”
Copper also conducts heat so heat passes from the machine and through the etched copper die to activate the foil and allow for the perfect release. The photo etching process is calculated the same regardless of the image so we can accurately figure out cost per piece.
“To me, the designer, the copper dies themselves resemble works of art,” Pienta says.
All of their copper dies are manufactured for them through Metal Magic, an engraver headquartered in Phoenix, Arizona that makes premium brass and copper dies for everything from stationery to wine labels, commercial packaging to annual reports, trading cards to book covers.
Pienta said Metal Magic is a great fit for Somersault.
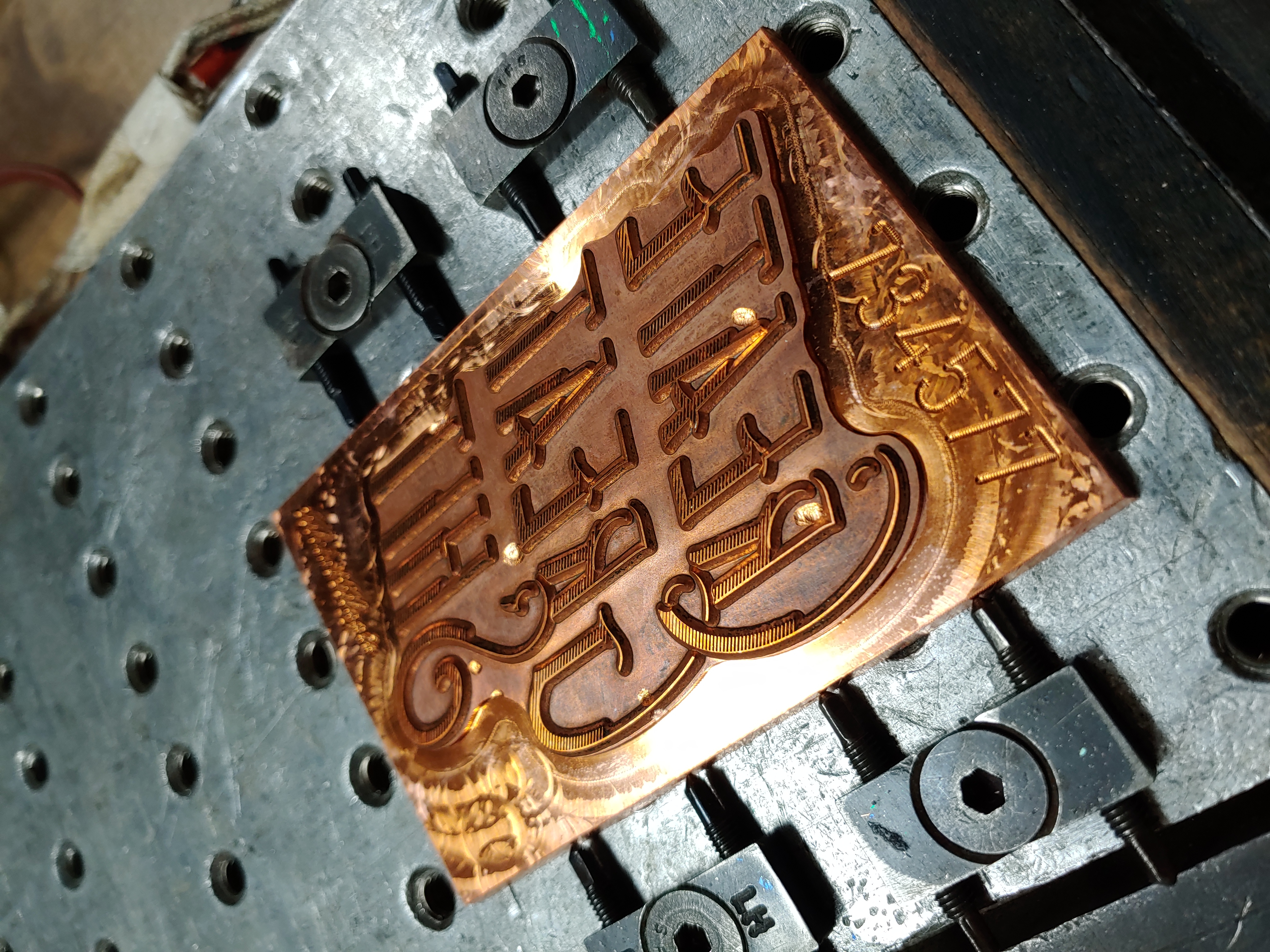
Copper letterpress plate created and used by Somersault Letterpress.
Photograph courtesy of Somersault Letterpress.
“They have been making copper and brass dies for over 30 years,” Pienta says. “We have been working with them for eight and appreciate and rely on their wealth of knowledge and expertise.”
It also doesn’t hurt, she added, that Metal Magic is a certified green supplier, powered by 100% solar and wind energy, and a Zero Discharge manufacturing plant.
“It’s a company we stand by,” she says.
Amy, a printer’s daughter from northeast Pennsylvania, and Mitch, a print salesman, worked together in Las Vegas. Mitch was a sales rep for a large commercial printer and Amy worked as a freelance designer.
“We both worked for clients like The Palms Casino and MGM Resorts International,” Pienta says. “We spent most of our time working together on high-end, complex event invitations until the financial crash in 2008. By 2010, both our positions had shifted to reflect the economic change and we were not doing near as much of what we loved anymore. So we took a chance and purchased our first Heidelberg Windmill from a friend and a colleague who were both retiring and did not want to sell their press to a large commercial printer.”
The time was right. Amy said their friend wanted someone to pick up where they left off.
“We wanted to be done with the commercial world and test our design and print strength on our own terms and with a new medium--letterpress printing,” Pienta recalls.
Somersault Letterpress was born in Las Vegas in 2011 and then moved East with them in 2015. “For eight years now, we have worked hand-in-hand at building a boutique print studio that offers truly custom, high-end letterpress printing for clients all over the country,” she says.
They settled in Jim Thorpe, a small tourist town tucked into mountain along the Lehigh River, named for the Native American Olympian who is buried there.
“The beauty of being in the historic downtown of Jim Thorpe is that we see a lot of visitors come to town looking to get away and see new things,” Amy said.” Our studio sits inside an old historic mansion on Broadway where people can actually see the presses at work. People are exposed to so few makers at work these days that it’s exciting for them to make the connection: ‘Oh wait, you USE those presses??’ “
Amy said visitors explore the shop full of only letterpress printed cards (no digital or conventionally printed cards allowed) made in their studio and by friends in the artisanal letterpress industry.
“They can see the wedding invitations displayed right there while watching the presses create even more,” Pienta says. “They can touch and feel the tactile difference of a letterpress printed piece. And they become so curious - they want to know what’s happening.”
Pienta said it’s exciting to engage with visitors.
“It’s exciting to see so many people light up, ask questions and appreciate that what we’re doing is not typical in any way, and it’s not easy - but it sure is beautiful,” she says. Somersault’s clients are those who look for something that will set them apart from the rest - an elegant, understated “wow factor.”
“They want a tangible representation of who they are,” Pienta says. “Our wedding couples want their invitations to be an extraordinary representation of their day and something their guests will hold on to. Our business clients want their clients see that they take their business very seriously.”
Clients’ and visitors’ excitement fuel Somersault’s innovation.
“Most of the challenges in our work come from pushing the envelope in design--using a new paper or something we’ve never printed on before or pushing the limits of size and image area,” Pienta says. “We enjoy trying new things so there’s a certain level of stress that goes along with that. But that also creates excitement as well. Each job we do - because they are so custom and because we're doing new and different things with almost each one - allows us to feel like there’s never a dull moment.”
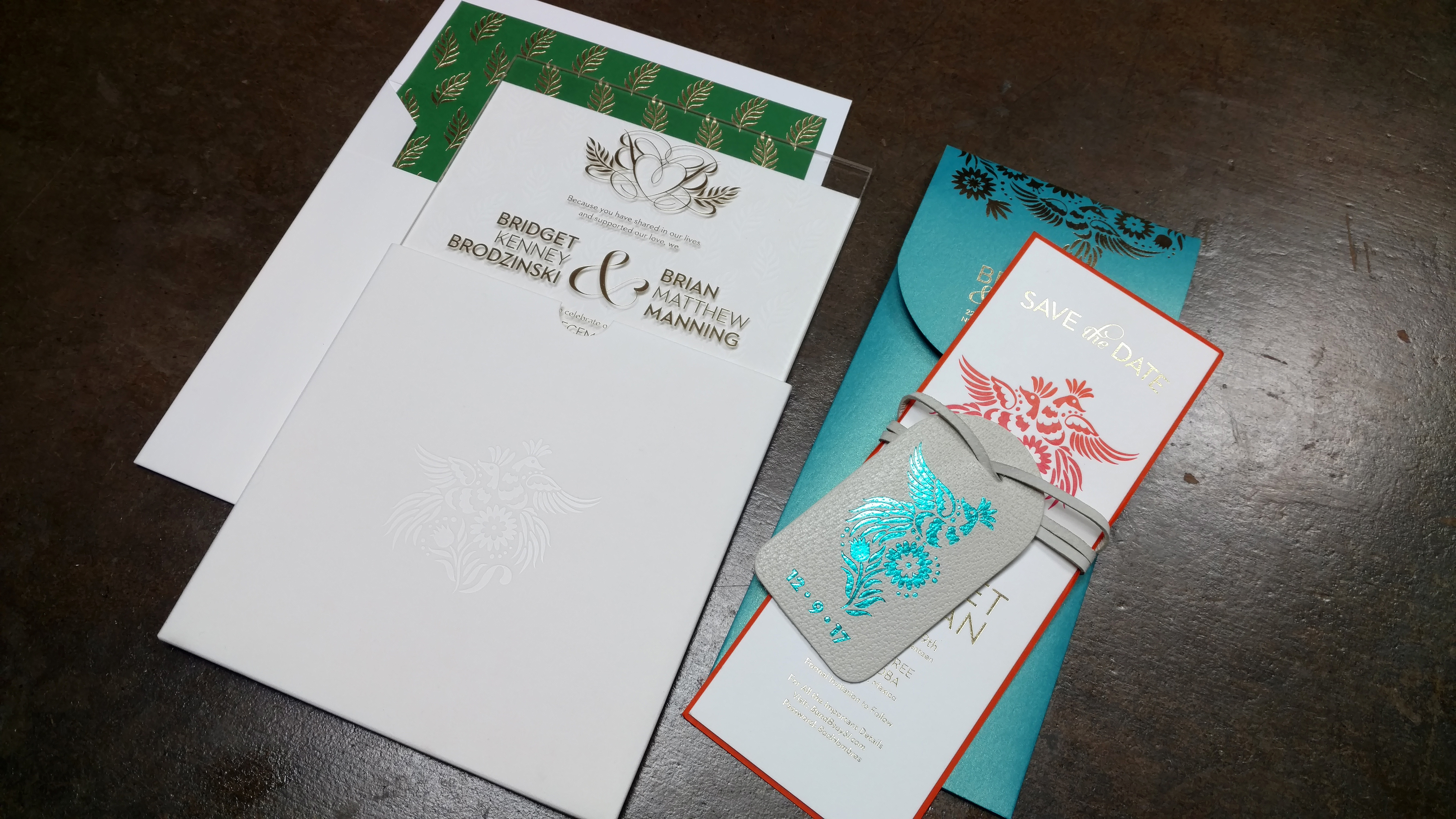
Photograph courtesy of Somersault Letterpress.
That’s a good day at work if you can walk away knowing even though it wasn’t easy, it was still enjoyable.
“I can honestly say we love what we do and look forward to the work every day,” she says.
Doing old-school printing in today’s day and age sets Somersault and its clients apart. Each year that Somersault entered work in the American Advertising Federation’s Awards Show they’ve received a coveted Judge’s Choice Award for letterpress printed work.
“That’s a huge testament to the fact that printed pieces are still making a difference. If someone says they can’t put it down or ‘I couldn’t throw it away’ that’s really effective marketing,” Pienta says. “That means something in today’s digital age.”
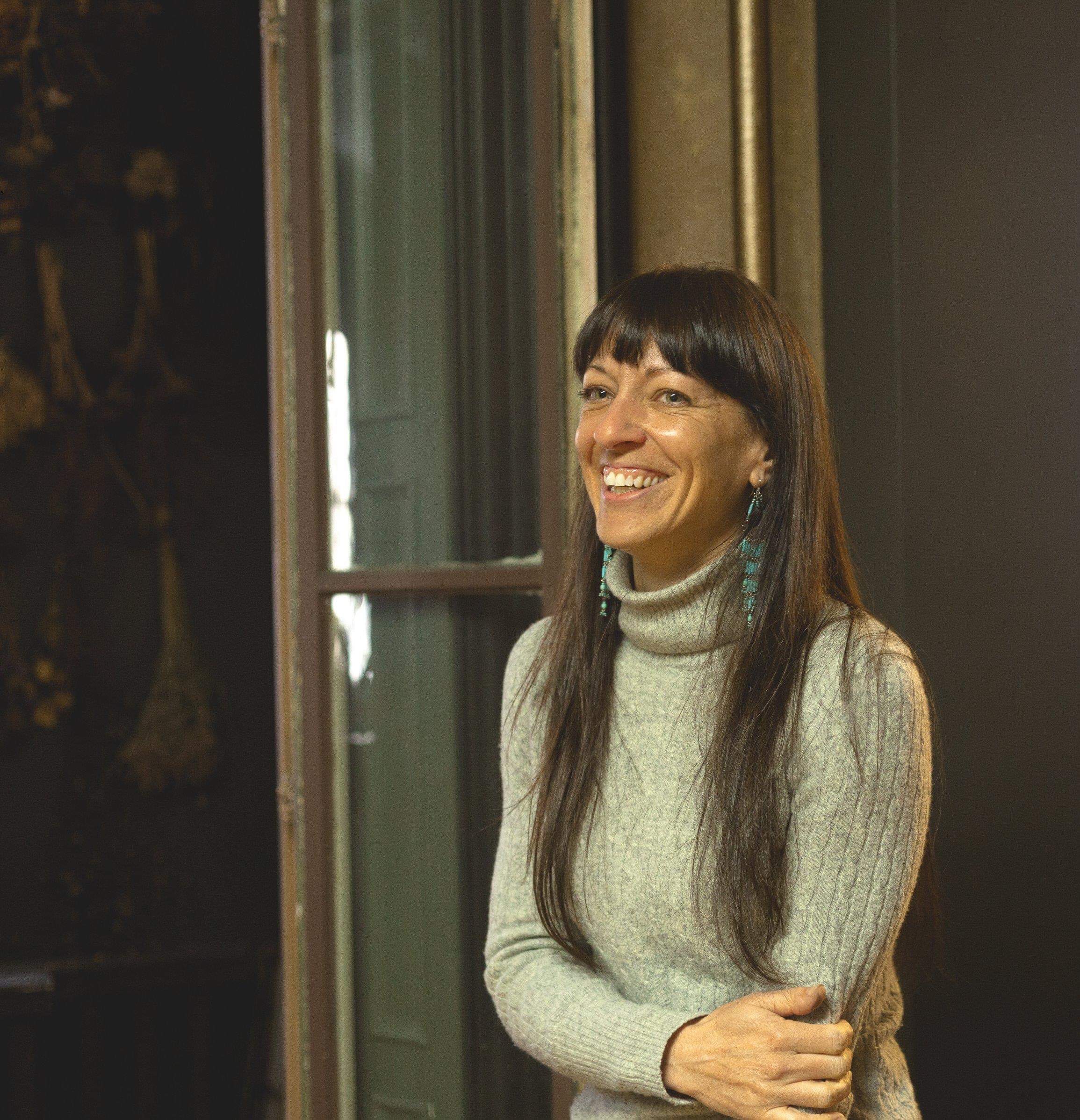
Photograph courtesy of Somersault Letterpress.
Pienta said they’ve had the opportunity to work with so many clients on such fun and inspiring projects, but there have been a few that were “just way too much fun from start to finish.”
The Guzman Star Wars wedding invitation included all different kinds of foil mixed with ink on double and triple thick paper stocks.
“Bringing the line drawings of the different ships to life through foil really made the images stand out,” Amy said.”The use of clear foil for the Death Star image gave it a very subtle and unique presence on the piece. Sometimes simplicity done well really retains elegance and that’s what we were shooting for with this invitation. Using hot foil and letterpress inks instead of full color images made for an upscale presentation.”
On the Vault 634 Gala Invitation, they used copper foil dies for all three colors on the plexiglass invitation - which was no easy task.
“This invitation also featured a sculpted, embossed lion head on the outer envelope that mimicked the three dimensional carvings found inside the venue,” Pienta says.
The Hakkasan Beverly Hills invitation featured foil on double thick black stock as well as a hot stamped dragon on felt paper to form the invitation sleeve.
“In this instance the copper die was used, but no foil,” Pienta says.”The copper was heated and just seared the felt flat in the press leaving an impression only.”
“It’s projects like these where we get excited to see what we can do with different substrates,” Pienta says. “In the end, it makes for some stunning and noteworthy event invitations or business cards to the point where our clients receive compliments on what they are sending out.
The couple would like to continue to grow their company.
“But not the kind of growth where we lose sight of what we do and who it’s for,” she says. “We want to stay small and stay focused, but also start to fold in employees that are as obsessed with details as we are, appreciate and respect the process, and look for their days to be more challenging than unchanging.”
The couple wants to keep pushing themselves to see what they can do with new and different ideas.
“Hopefully by the time everything comes full circle and we’ve established some deep, long-term roots here, we’ll be passing this knowledge and the process onto another lucky duo - like it was done with us - that will keep the art of letterpress printing alive and well for generations to come,” she says.
Resources:
Also in this Issue:
- Somersault Letterpress: Continuing the Legacy of Handcrafted Copper Letterpressing
- Transforming Copper Wires into Powerful Visual Statements
- HBS Copper: Continuing the Legacy of Handcrafted Copper Stills
- The Copper Art of Retablos
- SculptureCenter Unveils New Solo Show by Ektor Garcia