Fabitecture: Nature’s Beauty Mark on Copper
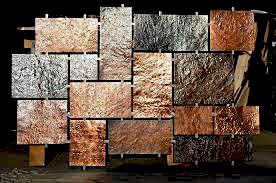
Photograph courtesy of Fabitecture.
Running the sculpture lab at the University of Wisconsin-Milwaukee for four years led Matthew Mabee to architecture and design before starting his business, Fabitecture, specializing in handcrafted custom furniture.
“I went back to get my Master’s in architecture and through that, it taught me more of design thinking,” he says.
Mabee found that he enjoyed making models and artifacts by hand.
“I was able to dedicate more time to my design style and my skills,” he says. “I was tinkering with furniture pieces.”
Mabee was first introduced to copper in 2009 by a professor who had a jewelry making and metalsmithing background and was helping to guide an architectural-based class.
“He liked copper because of the ease of forming it and manipulating it,” Mabee says.
The students were instructed to make a small-scale mockup of a building façade, which posed an opportunity for copper to come into play for Mabee for the first time.
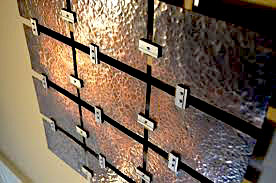
Photograph courtesy of Fabitecture.
“I partnered with a friend and we decided to make a hand-hammered copper wall panel,” he says. We left a natural finish and let it patina itself and thought we would let nature put it’s own beauty mark on it.”
He then became interested in experimenting with copper and how it relates to other metals.
“How maybe aluminum and copper have a nice contrast of color with them working together artistically and aesthetically,” he says.
Mabee also enjoys having a full range of patina options available to him when working with copper.
“I really like the liver of sulfur one — that is the one that has stuck with me,” he says. “The longer you leave it in, the darker it gets. It gets a rose kind of looking, purple reddish color.”
He also enjoys trying to predict and control what Mother Nature might do with his copper pieces over time.
“I could kind of determine what it would look like twenty years from now and if what I was building would still be aesthetically pleasing until then,” he says.
Later, he began using prototyping tools to allow him to perfect designs before making a prototype.
“I used parametric modeling, a virtual modeling software, so I could play with my designs before I built them and I could make more iterations using the computer,” he says.
It was the upcoming birth of his first son that was the initial motivation for Mabee to delve into handcrafting furniture pieces. He created a wooden bookshelf for his child’s room, using some steel components.
He decided to put the wooden piece with steel components online to see if anyone would bite.
“I sold it in two days and my wife got mad at me and I made another one and that sold and led me to making other things,” he says. ”People kept contacting me for custom sizes and finishes.”
This led the self-proclaimed functionalist to offer custom pieces for the home in addition to making decorative wall panels.
“The wall pieces are more sculptural art pieces,” he says.
Mabee lives in the small, artistic community of Cedarburg, Wisconsin where he works out of a small workshop that is attached to his home. He gets the most creative inspiration first thing in the morning when he gets out his sketchbook at his desk in his workshop and designs his latest shelf, coffee table, end table, dining room table, chairs, credenza or wall panel.
“I am really attracted to modern architecture and clean lines,” he says. “I get a lot of inspiration from modern building facades and different things happening in the architectural world.”
Most recently Mabee was asked to make a wooden coffee table with copper legs.He shares some of his greatest pleasures in working with copper.
“I could fix almost any mistake you could think of and reform it back to original condition and then rework what I was thinking,” he says.
“There aren’t many other materials with its luster you can bring out when you polish it and you can use sulfur to darken it.”
Etsy is the primary vehicle Mabee uses for sharing his work and taking custom orders he fulfills across the country.When he works on a piece for a customer, he approaches it as though he would want to display it in his own home.
“The compliment is when they get it in their home and uncrate it and are shocked at how it’s constructed and they order it again and again,” he says. “When a customer comes back is the best source of compliment. That makes me really proud of my work.”
Resources:
Also in this Issue:
- Torching Stories Told Through Copper
- Fabitecture: Nature’s Beauty Mark on Copper
- Koja Designs: Using Copper as a Canvas
- Recycling Mixed Metals to Create Beautiful, Unique Artwork
- French Sculptor Auguste Rodin Celebrated throughout North America and beyond with Rodin100 Tour