Download PDF Version [362 Kb]
- Speed is the Key
- High-Quality Power Important
- Diverting the Energy Stream
- Three Rods + "All Modes" SPDs
- It Worked
The world's largest independently owned agricultural seed producer had a serious problem. For lack of a simple thing like adequate grounding, the Harris Moran Seed Company faced the loss of several years of research and development and a threat to its competitive position.
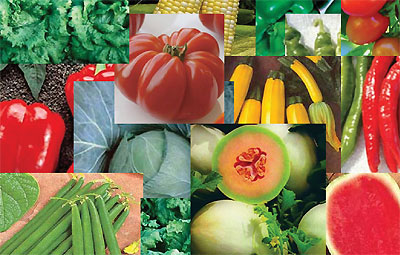
Speed is the Key
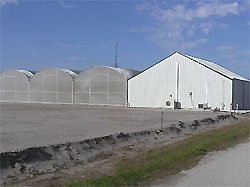
Agricultural seed breeding is very competitive. Staying ahead of the competition means bringing out a steady stream of new products faster than the other guy can.
But breeding seeds takes time. U.S. producers have to utilize on traditional selective breeding methods: plant, select, cross-pollinate, harvest and plant again, etc. The process takes up to seven crop cycles to produce an improved strain. Success depends on the work of skilled biologists and an uninterrupted string of crop cycles, each one building on the one before. Loss of a single cycle lengthens the time to market. Lose all in-process crops at once and several years of R&D go down the tubes.
To speed up the process, Harris Moran established a research station east of Ft. Meyers, Florida, where the climate allows two to three crops per year. The station consists of a laboratory, offices, a dozen greenhouses and several acres for controlled growing ( Figure 1). It is surrounded by a 30,000-acre tomato farm belonging to one of the Harris Moran's customers.
Back to TopHigh-Quality Power Important
Most of the station's time-sensitive breeding work takes place in greenhouses, in which thermostatically controlled evaporative coolers maintain the ideal 85° to 90°F growing range ( Figure 2). A 25-hp pump supplies cooling water from the farm's 60-ft well. The well also provides water to injectors and drip irrigation systems ( Figures 3 and 4). Those systems simultaneously feed water and nutrients at controlled rates to optimize growth. Sensors located throughout the facility supply data to computers that monitor and control the entire system.
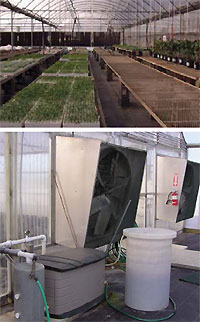
Figure 2. Time-sensitive breeding takes place in greenhouses (top), in which temperatures are controlled by fan-driven evaporative coolers (bottom) to maintain the ideal growing range. In the past, high-voltage surges destroyed the well pump that supplies the coolers, causing greenhouse temperatures to rise to 115° to 125° F and destroying several years' work in a single afternoon.
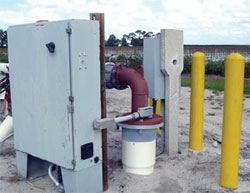
Figure 3. A 25-hp pump draws water from a 60-ft deep well at the Harris Moran Research Station. The well's plastic casing does not provide a natural grounding path. That fact, plus poor grounding elsewhere on the station led to several pump failures.
Because most process operations are both electronically controlled and motor-driven, the facility needs reliable, high-quality electric power. Unfortunately, that is precisely where the Harris Moran Research Station found itself in trouble.
Power supply wasn't the problem. When the grid goes off-line, the station's 200-kVA emergency generator ( Figure 5) takes over through an automatic transfer switch. Much more important is the quality of the incoming power, meaning, in Harris Moran's case, the absence of high-voltage surges.
In Florida, surges are mainly caused by lightning. Worse yet, electrical storms in the Sunshine State's notorious "lightning alley" peak between August and September, the most critical portion of the summer crop cycle. Lightning hasn't struck the research station itself yet, but it regularly strikes power lines on the local utility grid. When that happens, even miles away, high-voltage surges find their way into the research station's electrical system. It's those surges that threatened Harris Moran's competitiveness.
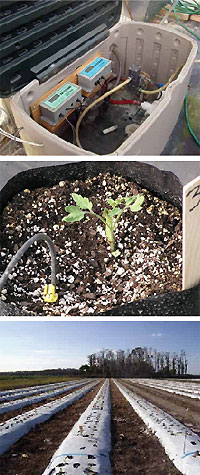
Figure 4. Injectors (top) supply irrigation and nutrients to seedlings (center) and seed crops (bottom). Highvoltage surges damaged this electronically controlled system.
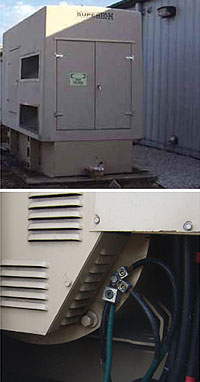
Figure 5. A 200-kVA emergency generator (top) powers the research station during outages. New, 1/0 AWG grounding conductors (green wires, bottom) were installed as part of a system-wide upgrade.
Tim O'Rourke was Harris Moran's Station Operations Manager during the period when the facility suffered its most costly electrical surges, and he understood the gravity of the problem. "A hit to the grid can cause $25,000-$30,000 in equipment loss and a lot of infrastructure damage," he said at the time, "but that's the minor aspect of the damage.
"When the well pump gets knocked out during the summer months and the evaporative coolers lose their water supply, greenhouse temperatures quickly rise to 115° to 120°F. Several years' work can be wiped out in an afternoon. That's the worst case scenario, and it has happened.
"A failure in the data collection and control system is almost as bad, and we had those, too. If the irrigators and nutrient injectors fail, plant growth is affected, but that's nothing compared with loss of a crop cycle."
O'Rourke called in his electrician, Jerry Phillips, President of Electrical Services Plus, LLC, a Naples-based contractor. Phillips recognized the power quality problem and brought in a PQ specialist, John West, founder and president of Power Systems Innovations, Inc. (PSI), headquartered in Orlando. PSI operates nationwide but is especially well known for grounding and power quality work in Florida. Together, the two set out to protect the seed farm from further damage.
Back to TopDiverting the Energy Stream
Their objective was to divert lightning-caused voltage spikes to earth before they could damage sensitive equipment downstream in the electrical system. That's normally done at the service entrance by way of a Code-required grounding electrode and some form of surge protection. There was no such protection on the service entrance, and it might not have worked even if it were in place, since the single rod electrode had a ground resistance greater than 150 ohms. That's high; significantly exceeding the 25-Ω limit cited in article 250 of the National Electrical Code® for a single electrode.
The important point here is that the National Electrical Code sets minimum standards based on safety, not power quality. In situations such as that at Harris Moran's research station, minimum Code compliance did not guarantee freedom from power quality problems.
High-voltage surges were able to enter the electrical system because the system provided a path of lower resistance than the path offered by the high-resistance electrode, plus its #4 conductor and whatever other resistance might have been present due to poor bonding.
Back to TopThree Rods + "All Modes" SPDs
Phillips began his system upgrade by driving three 24-ft copper-clad electrodes along one side of the main building roughly in a line between the service entrance and the facility's distribution transformer. The electrodes extend to bedrock and have a ground resistance slightly higher than four ohms. The station now had the basis for a proper grounding system.
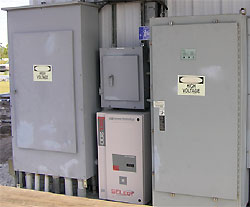
He then bonded the three new electrodes to the system grounding bus in the main service entrance panel, as required by Code, but instead of AWG #4, he used AWG 1/0. For good measure, he also ran and bonded AWG 1/0 to the emergency generator ( Figure 5) and distribution transformer.
For added protection, Phillips and West backed up the new grounding electrode with surge protection devices (SPDs) on every critical panel and sub-panel, plus one on the well pump. Lightning can get pretty powerful in Florida, so they selected a Current Technology SEL 200 unit for the main service entrance panel, Figure 6. The SEL 200 is rated at 200 kA line-to-neutral, line-to-ground, neutral-to-ground and line-to-line. Protection per phase is rated at 400 kA.
Surge suppression devices and all other types of voltage spike protection can only function properly when they are bonded to a low-resistance, low-impedance grounding system. Recommended practices suggest a maximum system ground resistance of five ohms.
Back to TopIt Worked
Phillips and West installed the new grounding and surge protection systems at the Harris Moran research station in 2008. Florida presented its usual flock of thunderstorms, and the storms probably sent the usual surges to the station, but not one of those surges made it past the service entrance. The new grounding and SPD system worked as planned. For the record, the upgrade cost approximately $18,000, of which less than a third included the installed cost of the heavy-gage copper grounding conductors. Considering the costs of potentially ruined equipment and possibly years of research saved, it was a bargain.
Back to TopThe Principals
Jerry Phillips is president of Electrical Services Plus, LLC, a full-service electrical contracting and consulting firm based in Naples, Florida. He is available at (239) 774-3146 or [email protected].
John West, Sr. is President of Power Systems & Innovations, Inc. (PSI), Orlando, Florida. Founded in 1992, PSI provides products, services and consulting related to power quality, power protection, surge protection, grounding, lightning protection and other anomalies that can damage equipment and/or cause data loss. He can be reached at [email protected], or (407) 380-9200.