It is not unusual for die castings to display some degree of porosity due to the rapid and turbulent flow of metal into the mold cavity. For most products, small amounts of porosity are tolerable from the standpoint of mechanical behavior, but the situation is quite different in the case of motor rotors. Here, porosity control is particularly important because even tiny voids can diminish the advantages offered by copper's high volumetric electrical conductivity. Large voids, which generally appear in the rotor's end rings, are also detrimental since they can make the rotor difficult to balance.
Early casting trials conducted by CDA found only 2%-3% porosity, chiefly in the ejector (far) end ring and virtually none in the conductor bars. A commercial manufacturer now in serial production (see French Die Caster Offers Copper Motor Rotors), has achieved even better results, with castings routinely exhibiting 99.5% of full density. However, larger rotors subsequently cast by CDA exhibited as much as 25% porosity in one ejector end ring and about 8%-10% in others. This was judged to be unacceptable, and CDA accordingly initiated a combined analytical-experimental program to determine the origin of the defects and develop steps to prevent them.
Walkington Engineering, a Wisconsin-based organization specializing in computational fluid dynamics, performed the analytical work, modeling the flow and solidification of copper within the mold. Simulation is faster and less costly than performing a lengthy series of casting trials. It can also suggest optimum process conditions, which can then be tested in a relatively small number of shots.
The trial rotor casting, Figure 1, consisted of the squirrel cage with its end rings and conductor bars, plus a system of gates and runners. The part is edge-gated with four approximately semicircular gates on each side of the vertical runner. Several other gating systems were modeled, but none showed significant advantages. The modeling program examined two important casting parameters: variations in the plunger position-speed profile (the shot profile) and the casting temperature.
The modeling software, Flow 3-D, was first tested by applying it to a shot profile that was known to have produced large voids in a 15-hp motor rotor. The profile is shown graphically in Figure 2; predicted and actual voids are shown in Figures 3 and 4, respectively.
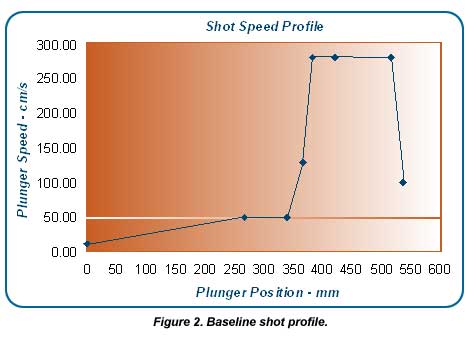
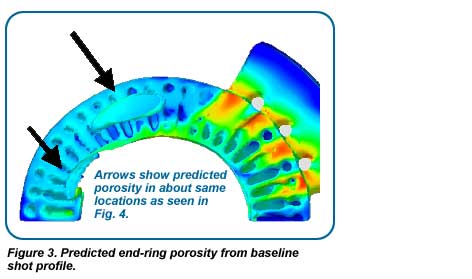
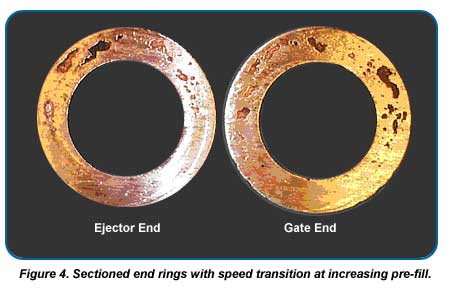
Having shown that the simulation successfully predicts conditions seen in actual casts, several modifications were made to the baseline profile in an attempt to reduce or eliminate porosity. The approaches taken involved pre-filling the initial portion of the mold relatively slowly, then accelerating the plunger for the remainder of the shot. It was felt that the less turbulent initial entry of metal might reduce the entrapment of voids later in the casting cycle.
In the first such simulation, the mold was filled to 20% (near the gates) at a plunger speed of only 25 cm/s before accelerating the plunger for the remainder of the shot. Two rates of acceleration were simulated, one to a uniform speed of 450 cm/s and one that ramped up from 220 cm/s to 500 cm/s. Neither regime would have worked, as modeling predicted formation of unacceptable voids.
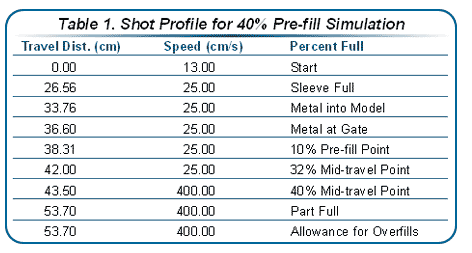
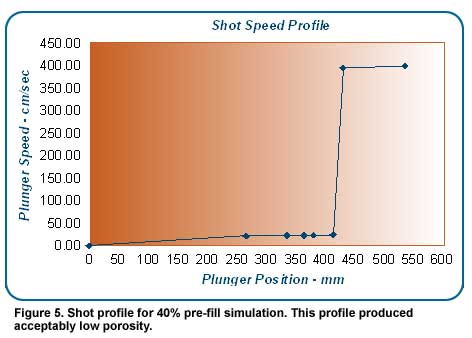
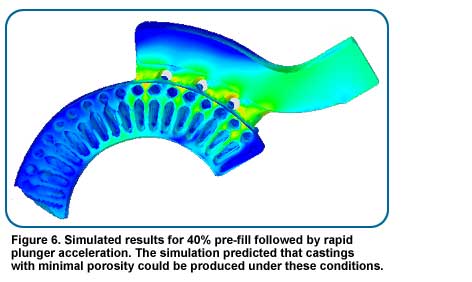
In the next simulation, the amount of pre-fill at the slow plunger speed was increased to 40%. The shot profile is described in Table 1 and Figure 5. The objective in this case was to accelerate the plunger while metal was filling the gate end ring. This scheme was based on some earlier simulations, which showed that a completely slow fill would have generated large bubbles later in the fill cycle. Modeling predicted that the new strategy would work, as can be seen in the simulation image shown in Figure 6. There are a few small bubbles but no large ones, and there is no porosity in the conductor bars.
Experimental Verification
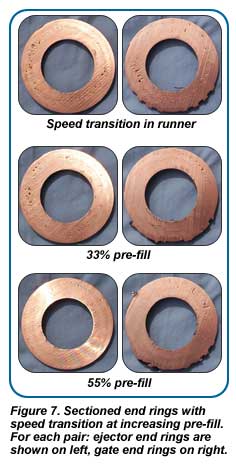
Several trial casts were then made with varying degrees of pre-fill. In the first cast, acceleration of the plunger began at a point at which metal had progressed about half-way up the runner. In the next two trials, metal was allowed to pre-fill 33% and 55% of the mold cavity, respectively. Results of these casting trials, shown in Figure 7, confirm predictions from modeling, i.e., that the degree of porosity decreases with the increase in pre-fill over the range of pre-fill investigated in the current study.
It is important to point out that casting trials were conducted using die pre-heat temperatures between about 240 F and 600 F (116 C and 316 C), a condition made necessary because of the sampling dies in use at the time. Subsequent tests were conducted with pre-heat temperatures around 1200 F (650 C), a temperature that had been shown to prevent early die failure due to heat checking. In fact, the higher temperature is now routinely applied in the commercial rotor die-casting process.
A few small voids are visible in end rings of castings made with 55% pre-fill; however, the defects are too small to prevent the ability to balance the rotors. The quality of these rotors was equivalent to the best achieved in other runs, and there was no apparent porosity trapped in the conductor bars.
Effect of Casting Temperature
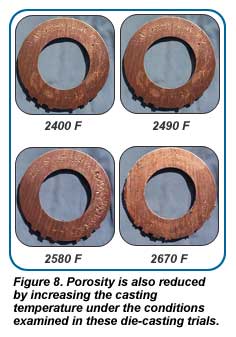
The final stage of the study involved investigation of the effect of casting temperature on casting quality. Figure 8 shows the degree of porosity found in end rings of rotors cast at 2400 F, 2490 F, 2580 F and 2670 F (1316 C, 1366 C, 1416 C and 1466 C). It is apparent that porosity decreases with increasing casting temperature. On the other hand, 2670 F is an extremely high temperature, and it is not expected that such superheat will be needed in commercial production, in which, as noted earlier, dies are preheated and maintained at 1200 F.
Conclusions Suggest Defects Can Be Avoided
It was shown that fluid-flow modeling is a useful, cost-effective and quite reliable tool for the prediction of void formation in die-cast copper rotors. Using this technique as the basis for casting trials, it was further shown that, when applied to the die set used in these experiments and at the temperature regime investigated, the incidence of both porosity in conductor bars and large voids in the end rings can be largely eliminated by pre-filling the die to some extent beyond the gates at a slow plunger speed, followed by rapid acceleration of the plunger for the remainder of the shot. Porosity and void formation are also reduced by increasing the casting temperature. Again, it should be pointed out that the much higher die temperatures used in commercial production may affect these conclusions, particularly with respect to the degree of superheat needed to ensure sound castings.