Other Headlines
At a copper motor rotor demonstration meeting in January, Darryl Van Son, consultant to the Copper Development Association (CDA), shared some of the most extensive data on copper rotor tests to date. Most notable were preliminary data that will help define the financial implications of switching to super-premium-efficient copper rotors.
What is the Cost of Efficiency?
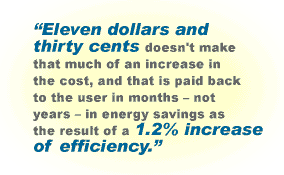
Van Son explained that the rotor conductor material - copper versus aluminum - presents the largest increase in cost when using the new copper motor rotor technology. Based on a 15 hp (11 kW) motor, material for a typical aluminum rotor currently costs roughly $4.00; whereas, copper rotor material costs roughly $14.00. To this, the costs of the energy associated with melting and die insert amortization are added. Die insert amortization accounts for the inserts only or, more specifically, only the parts that come into contact with molten copper during the process. Van Son says that's because the inserts are the only parts that would need to be replaced, as opposed to the whole master die. Insert replacement is based on an estimated 20,000-shot life.
"Roughly 65 cents goes to the electrical energy used to melt the copper. Another 65 cents goes to amortizing the die insert," Van Son says. "So we're up to about another $1.30 on top of the $10.00 (the additional cost of copper). But, this is a motor that lists at anywhere from $900 to $1,500, depending on enclosure. Now I admit, nobody pays list, but it puts into perspective that, for this type of product, even at wholesale, this is a very expensive motor. Approximately eleven dollars and thirty cents doesn't make that much of an increase in the cost. So, from a user's perspective, if we don't even try to cost-reduce the motor and just change out the aluminum for copper, that is paid back to the user in months - not years - in energy savings as the result of a 1.2% increase of efficiency on the nameplate (label on the motor detailing motor characteristics), if they use that motor for two shifts a day or more," he said.
Van Son also said that some manufacturers looked into how they could save money using this new die casting process to compensate for the added expense of the copper rotor. He said some have reduced costs using a variety of methods such as adjusting the stack length or changing rotor bar size. Cooling requirements were reduced, since copper naturally runs cooler than aluminum. However, the biggest cost reduction resulted from optimizing the motor around the copper rotor. In an optimized motor, rotor losses were down 40%, and total losses were reduced by 23%. Temperature rise was reduced by 41%. "We added 1.6% to the nameplate. Whereas, just a straight change out from aluminum to copper added 1.2%."
A Consistent Pattern
Van Son attained his data from a variety of sources. Data were taken from the copper motor project's own trials but were also gathered from various manufacturers who replaced copper with aluminum in their own rotors. What emerged was a definitive pattern of improved efficiency over a wide range of motors. "From 3 kilowatts to 200 kilowatts, the consistency in the reduction of losses was within a predictable pattern. Theoretically, we looked at anywhere from 12-20% reduction in losses as the result of a rotor that is twice as conductive, or has half the resistance. And the pattern fits. Even though the range of efficiency here is not all that consistent, the difference is what is consistent, and it is predictable. You would expect to have loss reductions higher at the small sizes, and smaller at the large sizes, and that is the exact pattern we're seeing here," he explained. (See Figure 1.)
Figure 1. Motor Efficiency: Copper vs. Aluminum | ||||||
---|---|---|---|---|---|---|
hp | kW | Poles | Efficiency | Difference | Loss Reduction | |
Al | Cu | |||||
4.0 | 3.0 | 4 | 83.2 | 86.4 | 3.2 | 19.0% |
7.5 | 5.5 | 4 | 74.0 | 79.0 | 5.0 | 19.2% |
10.0 | 7.5 | 4 | 85.0 | 86.5 | 1.5 | 10.0% |
15.0 | 11.0 | 4 | 89.5 | 90.7 | 1.2 | 11.4% |
25.0 | 19.0 | 4 | 90.9 | 92.5 | 1.6 | 17.6% |
40.0 | 30.0 | 4 | 88.8 | 90.1 | 1.3 | 11.6% |
120.0 | 90.0 | 2 | 91.4 | 92.8 | 1.4 | 16.3% |
270.0 | 200.0 | 4 | 92.0 | 93.0 | 1.0 | 12.5% |
Average: 14.7% |
In one group of experiments, a number of variables were changed from rotor to rotor. And from those tests, once again, a predictable pattern emerged. "This was our chance to experiment with the consistency and the range of pressures and die casting variables, including quenching - air-cooled versus water - quenched," Van Son explained. "What we found on this group of identical rotors was that the range was so tight on efficiency levels. The watts lost were an average of 157. The low was 153; the high was 167. These are extremely consistent results over a number of rotors."
In the same tests, stray load losses were reduced 23%. Van Son attributed that to the consistency of the performance of the copper rotors. "Theoretically, the conductivity of a rotor shouldn't have that much effect on stray load," he explained. "But what we believe is, the consistency of these rotors - that is to say the reduction in porosity and the like - was able to reduce those stray load losses."
Additional Implications
As different manufacturers have different needs, the implications of the data gathered from the copper motor rotor trials can be applied to several scenarios. "You can go for higher efficiency in the same stack, in order to have the highest efficiency out there," he explained. "Another possibility is to keep same the efficiency and reduce the stack in order to offset the cost of the copper. Or, something in between. And that's really what we're seeing from those who have modified the rest of the motor design. They're trying to achieve a balance."
"No two manufacturers have the same motivations. They don't have the same markets. They don't have the same applications. And they don't have the same economics," Van Son said. "But, what we've been able to learn from all these different manufacturers is that there are clearly possibilities by utilizing this technology as a competitive tool in the new marketplace."