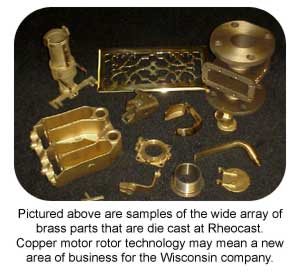
Although interest in the technology of die casting copper motor rotors continues to gain momentum, motor manufacturers remain cautious about making the investment necessary to bring the technology in-house. By outsourcing the casting of the rotors, these manufacturers can evaluate the feasibility and associated economics of the new technology at a much lower cost, giving companies like the Rheocast Company, a brass die casting operation in Germantown, Wisconsin, a potential new area of business.
Rheocast has been die casting brass for over 30 years and is one of only a handful of operations to do so. The company's client list includes General Motors, General Electric, Black and Decker, and Ingersol-Rand. They manufacture a wide array of products from architectural hardware to plumbing and electric motor components. "To this point in time, Rheocast has specialized exclusively in the art of die casting brass," explains vice president of manufacturing, Mark Morton. "This is a new endeavor for us. The emerging interest in copper for motors coupled with new developments for preserving tooling under extreme heat conditions opens a new opportunity."
According to Morton, Rheocast has been intensely interested in the copper motor rotor since learning of the project's successful efforts in extending tool life. When a member of his staff attended CDA's copper motor rotor demonstration meeting in January, he found a reason to explore further the die casting of copper: potential customers. "These companies are about the business of developing premium-efficiency electric motors," Morton explained. "If the process can be perfected and made commercially and economically feasible, then I believe there will be a very real motivation for manufacturers, industrial consumers and private consumers to take advantage of this new technology."
In order to accommodate potential new clients, Rheocast will be making some adjustments to its current machinery. "Presently, we are equipped for working with brass. While this is similar, the higher melting temperatures and oxidation tendencies of copper will necessitate upscaling some equipment. We envision a dedicated cell for bringing copper projects into production," Morton said.
Customization is familiar to Rheocast, as most of the parts they presently manufacture are custom-tailored to client specifications. "We help our customers develop their specifications to complement the die cast process," Morton explained. "For this project our objective will be to utilize the collective resources of the Fall River Group (Rheocast's parent company) to develop a high-tech, turnkey product of very close tolerances. The desired outcome will produce a component of even greater efficiency to optimize further the gains in the finished product. We will definitely bring all our experience and engineering capability to the task."
Morton feels cast copper heat sinks could be used in cooling electronic components, such as voltage rectifiers, or hardening large microchips for severe industrial environments or high-wattage power supplies, to name a few. "I feel potential markets may exist in the fields of industry, computer technology and transportation," he said.
Whether casting motor rotors, heat sinks or any other application that can benefit from this new process, Morton feels the impact of the copper die casting process on the die casting industry, in whole, remains to be seen. "I imagine a great deal of activity over the course of the next seven years for the die casting houses who are prepared to make the commitments required to cast copper. The impact on our industry after that point, as related to the motors campaign, will depend on whether manufacturers elect to make the component themselves or continue to outsource that activity."