Despite the economic and environmental benefits of switching to copper motor rotors, cast copper rotors have yet to be commercialized. Advanced Energy, an independent nonprofit organization in Raleigh, North Carolina, hopes to propel this new technology from the testing lab to the factory floor.
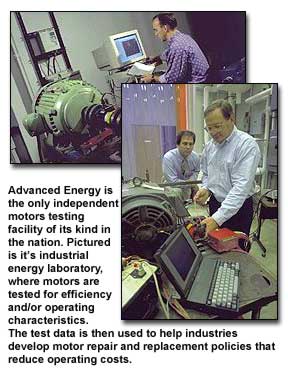
"This project fits directly into our mission of creating economic and environmental benefits through innovative approaches to energy use," explained Kitt Butler, business development manager at Advanced Energy. "Also, as a leader in motor efficiency education to industrial motor users, this technology appears to have great potential, and we want to make certain our customers are aware of the possibilities."
The role of Advanced Energy in the copper motor rotor project will be to further test and promote the technology. "To date, a wonderful amount of work has been done by the Copper Development Association (CDA) to develop and demonstrate to motor manufacturers that copper rotors are feasible. Also, from what I could see in Denver [at the recent demonstration meeting], motor manufacturers and vendors to the industry are taking notice. This is great news for our economy, as one part of this equation, the supply side, is being addressed very well by this effort," Butler explained. "The other side of the equation is the demand side, or the motor users. Having the ability to manufacture new, more-efficient motors does not always mean that the market is ready to run out and buy them. 'Build it and they will come' works in Hollywood but does not always play in reality. Motor users need to be educated on life-cycle costs and payback periods so they can make informed and better decisions."
The North Carolina Utilities Commission founded Advanced Energy in 1980 under the name Alternative Energy Corporation (AEC). The company was formed in response to rising electricity rates at the time due to an increase in power plant construction. The role of AEC was to explore alternative ways of producing electricity and to discover ways to get more work out of the electricity already available. The name was officially changed in 1996 to Advanced Energy, to reflect the expanded role of the corporation in promoting energy efficiency technologies. In this capacity, Advanced Energy works with a wide array of businesses and industries on many different levels.
Regarding motors, Mr. Butler explains, "We help motor manufacturers achieve regulatory compliance with the EPCA (Energy Policy and Conservation Act of 1992) through consulting and testing. In fact, over the past 18 months, we have consulted on 24 of the 30 Compliance Certificates issued thus far by the Department of Energy to motor manufacturers selling 1-200 hp, 3-phase, 2-, 4-, and 6-pole motors in the United States."
The potential for energy savings using cast copper rotors makes the copper motor rotor project of particular interest to Advanced Energy. "The Energy Policy Act of 1992 set the standards for industrial motor efficiency in our country mandating specific, minimum efficiency levels for motors between 1-200hp. The motor industry, through the National Electrical Manufacturers Association (NEMA), responded positively last June with a definition of premium efficiency when they rolled out the NEMA PremiumTM program. These motors are essentially the best you can buy from an efficiency standpoint. Copper-rotor motors may have an opportunity to raise the bar even higher," according to Butler.
Dr. John Cowie, vice president of strip, sheet and plate at CDA and program manager of the copper motor rotor project, welcomes the help of Advanced Energy, "We are now in the technology transfer phase of the project and are moving toward the promotion phase. But, before we can start the promotion, we need to partner with companies like Advanced Energy who can provide considerable assistance through their membership." he said.
From a technological standpoint, the testing of copper motor rotors at Advanced Energy will go a step further than any trials to date. "We see two potentially critical needs that have been only slightly addressed so far in regard to testing," Butler said. "First, we want to be able to clearly demonstrate the benefits that copper has versus aluminum with regard to rotors. We would like to test multiple copper rotors alongside aluminum rotors inside a common stator. We would want to control the inputs so that the data can have as much credibility as possible. Stack length, lamination design, slot sizes, air gap, etc., need to be the same across the board between aluminum and copper, so that we can compare apples to apples. From this testing we would be able to make statements about the results that, to date, the motor-using public has never heard. Efficiency, torque, temperature rise, current unbalance and speed accuracy would all be topics for review from these tests."
Dr. Cowie hopes to begin working with Advanced Energy within the next few months. "Independent verification of our motor test results by a respected laboratory such as Advanced Energy would go a long way in convincing motor companies to invest in copper die casting equipment" he said.