Induction furnaces are normally used for the melting of copper, due to its higher melting temperature of 1083°C (1981°F). The following two styles of induction furnaces are suggested for copper rotor die-casting:
- Double push-up furnaces are recommended when prototyping or small scale production is planned, although they can also be used for larger-scale production.
- Tilting furnaces are also recommended for larger-scale, continuous manufacturing.
These furnaces are described below.
9.4.1 Double Push-Up Furnaces
Double push-up furnaces use the approach of single-shot melting. As shown in Figure 9.4.1.1, single shot melting rapidly melts enough metal for only one shot, and then the melting process is repeated for the next shot. The obvious advantage of this approach is that the melting process can be rapidly started or stopped, providing flexibility when only producing a limited number of rotors.
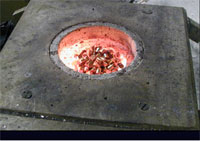
A double push-up furnace is used to increase the productivity of single-shot melting (see Figure 9.4.1.2). This style of furnace has two crucibles, both heated from a single induction power unit. Each crucible is surrounded by an induction coil, and sits on a ceramic pedestal that can be raised by a pneumatically-powered cylinder. The power is transferred backwards and forwards between the two coils. Once the copper in the first coil has been melted, the cylinder pushes the crucible out of the coil, to allow the liquid copper to be transferred to the die-casting machine (see Figure 9.4.1.3). In a matter of seconds, the induction power can be transferred to the second coil, to start melting the copper in that coil.
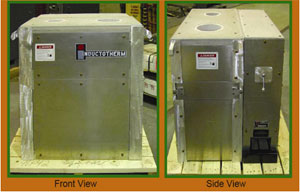
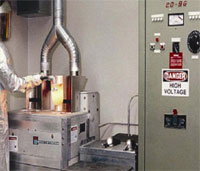
Due to the smaller size of the crucibles used for single-shot melting, sheared cathode is not typically used as the melt stock. Instead, chopped copper wire rod provides an increased surface area and better packing density, leading to more rapid melting. The copper rod in the crucible shown in Figure 9.4.1.1 is approximately 12.5 mm ( -inch) diameter chopped into lengths of about 19 mm (-inch). Such chopped rod is often widely available around the world, and is only marginally more expensive than sheared cathode.
The double push-up style of furnaces can provide the cycle rate required for rotor die-casting. During development trials, a 60kW induction power source was shown to be capable of melting 3.6 kg (8-lbs) of chopped copper rod in less than two minutes. Rotors requiring a shot weight larger than 3.6 kg would simply use a bigger induction power unit to meet the targeted cycle rate (typically 2 to 2 minutes for rotor casting). Double push-up furnaces can be purchased in a range of sizes meeting the throughput required of most copper rotors.
As the melting time used for single shot melting is very short, it may not be necessary to use a cover gas to prevent oxygen pick-up by the liquid copper. However, if a cover gas proves necessary, a blanket of inert gas (typically nitrogen) or reducing gas (nitrogen with 5% hydrogen added) can readily be applied to the top of each crucible.
9.4.2 Tilting Furnaces
For the high productivity associated with continuous production, it is recommended that a tilting furnace be used. In this approach, a larger amount of copper is melted in the style of induction furnace shown in Figure 9.4.2.1. The larger crucible size allows greater flexibility in the choice of charge material, including sheared copper cathode, high quality electrical grade copper scrap, shop run around scrap (biscuits and runners), or chopped wire rod. To protect the liquid copper from oxygen pick-up, a metal or ceramic cover is placed on top of the crucible, and a melt cover of nitrogen-5% hydrogen applied to the top of the liquid bath.
Once the liquid copper is at the correct temperature, the furnace is tilted hydraulically to pour a controlled amount of liquid copper into a ceramic cup (see Figure 9.4.2.2). A robot is then used to pick-up the cup and transfer the liquid copper to the shot sleeve of the die-casting machine.
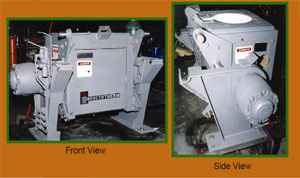
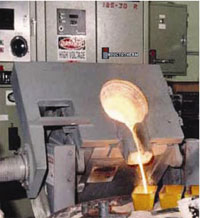