Although the most celebrated copper alloy coin - the brass farthing - never existed, both the pure and alloyed metal have, with silver coins, formed the basis of the British coinage. Queen Elizabeth would never agree to a copper currency, but she did allow copper token money towards the end of her reign. It fell into disfavour, however, and James I prohibited tokens altogether. In 1613 he gave authority to Lord Harington to issue some more or less experimental copper farthings; but the first real British copper currency dates from 1672, when a halfpenny and a farthing were minted. These were made of pure Swedish copper, with 175 grs. to the halfpenny and 87 1/2 grs. to the farthing. All these coins were produced by the old-fashioned method of hammering which was not supplanted until after the invention of the stamping press a century later. The Isle of Man had its own copper currency in the Stuart period, with farthings and halfpence bearing the island's three-legged symbol. It continued to issue its own money until 1864.
Throughout the ages governments have, on the whole, honestly sought to maintain the value of the coinage except when debasement was deemed part of the royal prerogative. A constant struggle has been waged against counterfeiters who found a ready means of illegal profit both by clipping and by substituting base metal. During the middle of the 18th Century the tremendous increase in counterfeiting in England created a scandal. The Birmingham district was the centre of this malpractice, notably in respect of copper; very severe penalties were exacted and dead counterfeiters were constantly seen to be swinging from the gibbets on Handsworth Heath.
Matthew Boulton - the partner and supporter of James Watt - was one of the men responsible for the further development of a copper coinage. Boulton was, in fact, one of the first 'industrialists'. He acquired a large interest in the copper and tin mines, and, as he was a staunch believer in an honest currency, he devoted much thought and skill to perfecting a coining press. Copper money was by that time almost out of circulation, and so great was the shortage that various manufacturers were allowed to issue token money (Fig. 33).
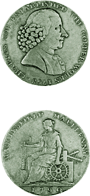
By means of a special collar applied to the dies, Boulton succeeded in producing coins of a standard size and weight which exactly fitted a tubular gauge; this enabled spurious money to be detected instantly by its weight alone. He then started to manufacture for abroad coins of such excellence that the Government promised him a contract to mint pennies; but the Royal Mint succeeded, by passive resistance, in delaying the order for ten years, until 1797. Meanwhile, Boulton continued to mint copper in large quantities, including his token money, the famous Boulton penny. At one date he even outran the supply of raw copper. His description of his own mint at Soho, Birmingham, in 1792 is interesting:
'This mint consists of eight large coining machines, which are sufficiently strong to coin the largest money in current use, or even medals; and each machine is capable of being adjusted in a few minutes so as to strike any number of pieces from 50 to 120 per minute. Each piece being struck in a steel collar, the whole number are perfectly round and of equal diameter.' (24)
Boulton's presses could manufacture as much as 1,200 tons of coins a year. His first official contract for the British Government was for twopenny pieces, pennies, halfpennies and farthings. It amounted to 4,200 tons between 1797 and 1806. An interesting footnote concerning the Boulton penny relates to the practice of adding these coins to molten iron when 'specially good metal was required'. This foreshadowed modern metallurgical developments, in which controlled amounts of copper are added to cast iron to improve strength, corrosion resistance and machinability. Boulton also issued some very fine medals in bronze and the precious metals, employing in their design only artists of the highest calibre such as Flaxman.