High Strength Copper Alloys Boost Injection Molding
Higher production rates are making copper alloys, which transfer heat rapidly, the materials of choice for many injection and blow molds for plastics. In molding, there's a major economic advantage to rapid removal of heat from the molten plastic: it raises production rates and reduces part defects. This more than compensates for the slightly higher cost of copper alloys - a difference likely to add no more than five percent to the total cost of the mold tool.
Besides cutting costs, high thermal-conductivity copper alloys offer these advantages in molding:
- More uniform heating.
- In some instances, tight dimensional specifications in large, complicated plastic parts can be achieved only if the parts are made in copper-alloy molds.
- Improved esthetics because fewer "sink marks" and other defects are created. As a result, lower injection and pack pressures can be used, saving material.
- Large plastic parts cast in copper-alloy molds exhibit much less warping; the excessive warping associated with parts made in steel molds can make it difficult to assemble large parts into systems.
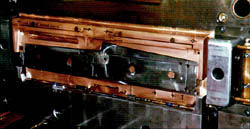
Complex plastic bexels for Whirlpool washing machines are produced from a copper alloy mold. Advantages include improved part surface quality, little or no warping, closer adherence to dimensional specifications, higher production rates and lower overall cost of manufacture.
In molding, copper alloys are replacing the commonly used mold steels, such as Type 420 stainless steel, because they have thermal conductivity three to nine times higher. Yet, the alloys are hard enough to meet the wear requirements of manufacturers aiming for high production rates of injection molded parts.
For instance, "high hardness copper beryllium, C17200, has a Rockwell hardness of C41, approaching that of steels. Wear resistance is often associated with hardness in the toolmakers' mind. Copper alloy have been shown to provide hundreds of thousands of production cycles.
Because wear resistance is more of a surface hardness phenomenon, a number of coating systems provide hard surfaces which extend the life of copper alloy molds - giving the best of both worlds: excellent heat transfer and good wear resistance.
The copper alloys, which include the nickel-silicon chromium-hardened high strength, high-conductivity alloy, C18000, developed by Ampco Metals, are commonly used in the creation of very large components by injection molding.
A copper be beryllium alloy used to make the molds for injection molding of the polypropylene bumpers for Renault in France was supplied by Materion Corporation (formally Brush Wellman), according to sales manager J. Scott Smyers. A number of U.S. suppliers are producing and stocking the copper berylliums and the C18000 alloy in both rod and heavy plate forms.
Molds often include a core to shape the parts and to speed cooling. Cast C82500 copper beryllium is an option for these cores. Sometimes, copper cores are used with steel molds, according to Truman Moore, president of TriCast Corporation, Crystal Lake, Illinois, which fabricates copper-alloy molds and their parts by a liquid casting process.
An industry task force under the auspices of the Copper Development Association has been introducing this array of advantageous alloys to the plastics industry for the past two years at trade shows, technical symposiums and at manufacturing sites throughout the U.S.
Wedges, lifters and slides are other required parts for molds. They are often made of aluminum bronze alloys C61900 and C62500. Pins and cores are often fabricated from nickel-silicon-hardened alloy, C64700.
Ampco Metal, Inc.: 800/844-6008
Ansonia Copper & Brass: 800/521-1703
Materion Corporation (formally Brush Wellman): 216/383-6835
Hussey Marine Alloys Ltd.: 800/767-0550
NGK Metals Corporation: 610/921-5000
Revere Copper Products, Inc.: 800/448-1776
SIPI Metals Corporation: 800/621-8013
Speciolly, Inc: 773/376-0100
TriCast: 815/459-1820
Also in this Issue:
- High Strength Copper Alloys Boost Injection Molding
- Bronzes: Copper Alloys that Counter Friction
- Copper Enhances Communications
- Copper Ensures More Hot Water
- Fashionable Facilities Count on Copper Cachet